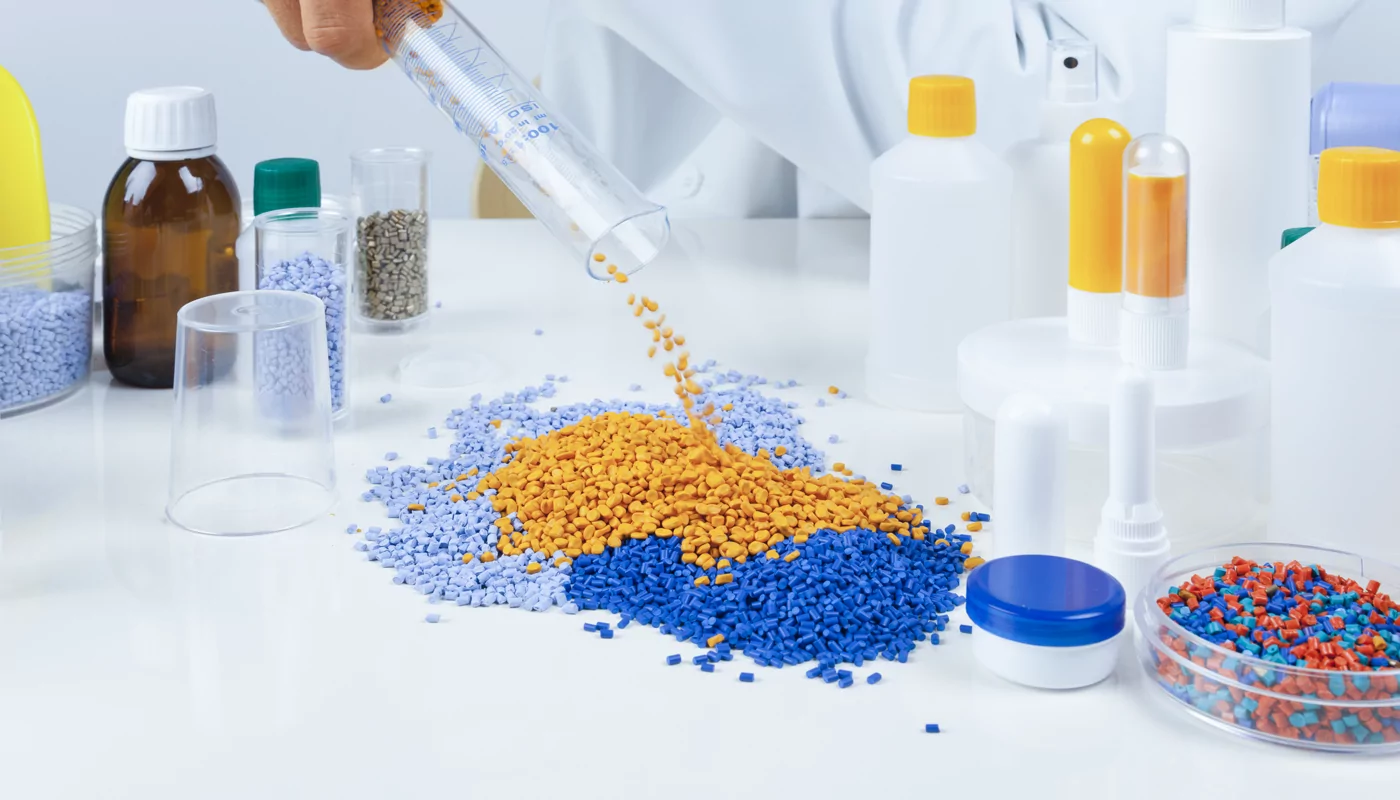
Polymerization
Modern Mixing Solutions for Sensitive Processes
Emulsionspolymerization
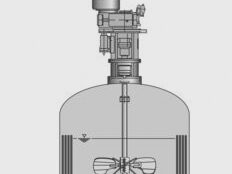
Solvent Polymerization
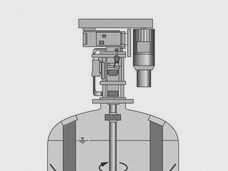
Suspension Polymerization
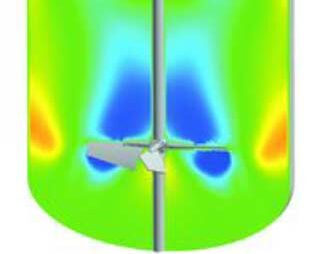
There are two different types of suspension polymerization
- Pearl polymerization: neither the polymer nor the monomer are soluble in the carrier liquid so that polymerization takes place inside the monomer droplets (diameter 10–1000 μm).
- Precipitation polymerization: the monomer is dissolved in the carrier liquid, whereas the polymer is not soluble and thus precipitates during polymerization.
Primary polymer particles usually have a diameter of approx. 1 μm. These particles agglomerate to porous secondary particles with a diameter of 100–200 μm. The solid particles have a tendency to stick together (coagulate) in certain polymerization phases and thus have to be separated again by shear forces in a flow field.
HIPS (High Impact Resistant Polystyrene)
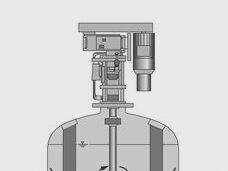
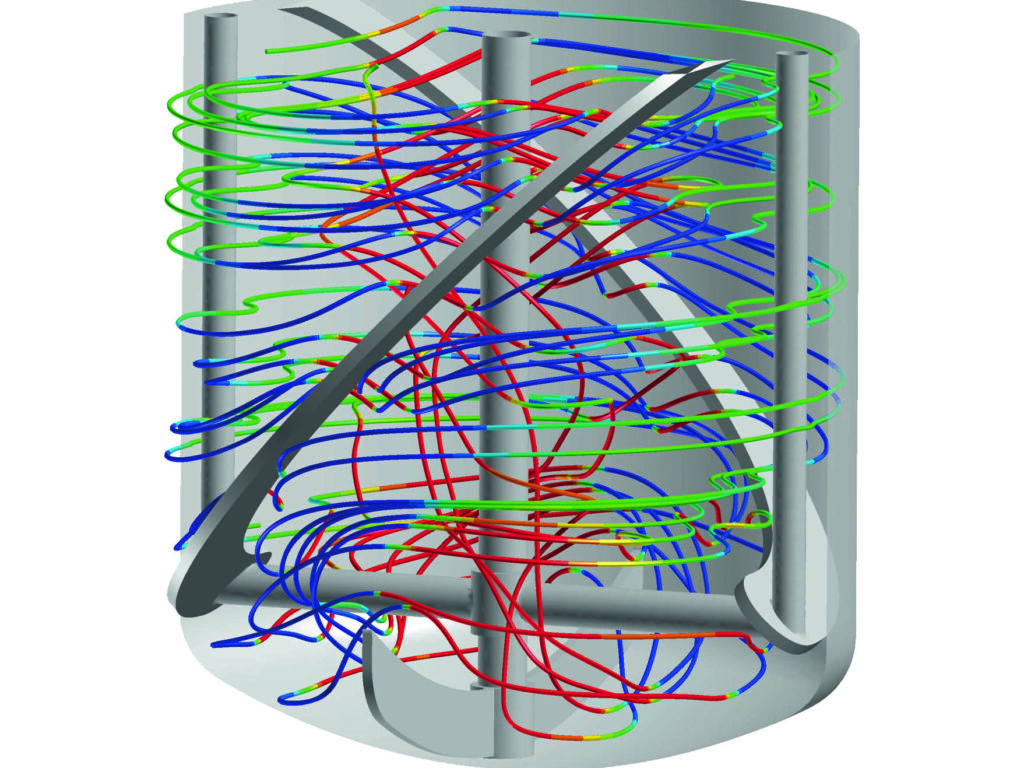
Rubber
Polybutatien (Butyl Rubber)
Polybutadiene (butyl rubber) is used as a synthetic rubber, particularly for the treads of car tyres. It is almost exclusively produced by solution polymerization using Ziegler-Natta catalysts. Toluene is the most commonly used solvent. The mixing requirements for the reaction are good homogenization and axial flow to ensure rapid equalization of concentration and temperature gradients.
IIR (Isobutene-Isoprene Rubber)
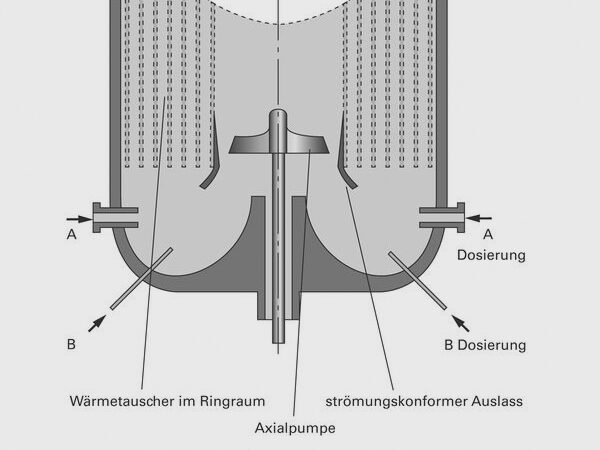
Polyester and PET (Polyethylenterephthalat)
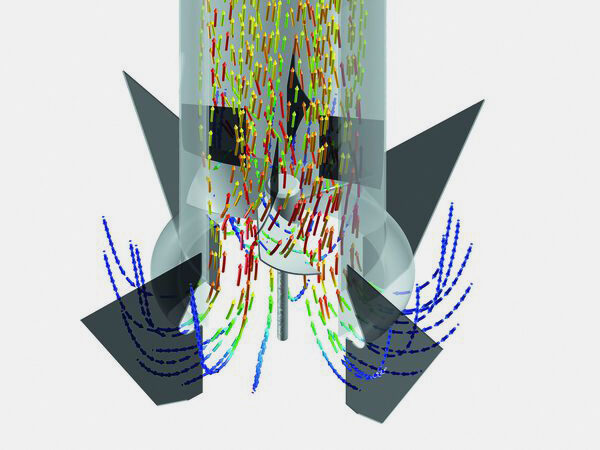
HDPE (High-Density Polyethylen)
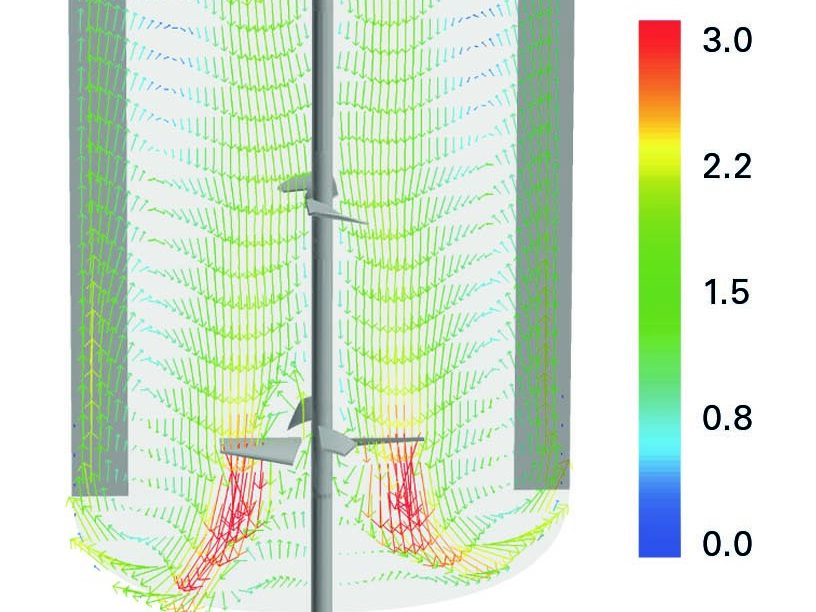
EPS, PMMA, PVC
Some of the most common polymers, such as Polyvinyl Chloride, Expanded Polystyrene and Polymethyl Methacrylate, are synthesized using pearl polymerization. Pearl polymerization is characterized by the monomer being present in an insoluble form at the start of polymerization. The monomer droplets are dispersed in the aqueous phase and act as “small water-cooled reactors”.
Key parameters governing the product quality during pearl polymerization are the particle size distribution and often also the porosity of the end product. As a general rule, the material with the narrower particle size distribution is more attractive to the market. This goal means demanding requirements for the mixing system:
- Narrow droplet size distribution of the monomer in water
- Small temperature and concentration gradients
- Avoiding of a separate monomer phase on the surface (pooling)
- Homogeneous suspending of the polymer beads
- Good heat transfer
Pearl polymerization is generally carried out with simple, usually single-stage radial-pumping impellers. Particularly in tall vessels, however, their mixing efficiency is limited in the upper regions. The advantages of the Ekato Viscoprop agitator over these traditional mixing systems are discussed below.
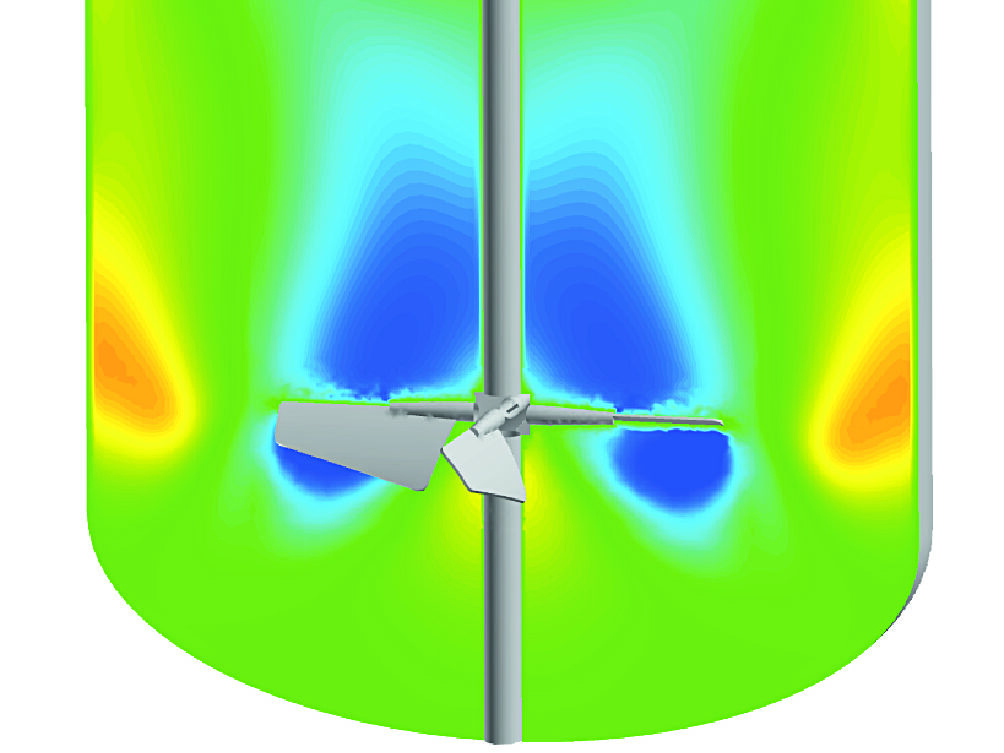
ABS (Acrylonitrile-Butadiene-Styrenecopolymer)
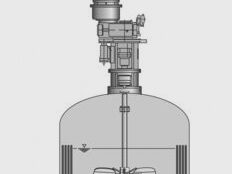
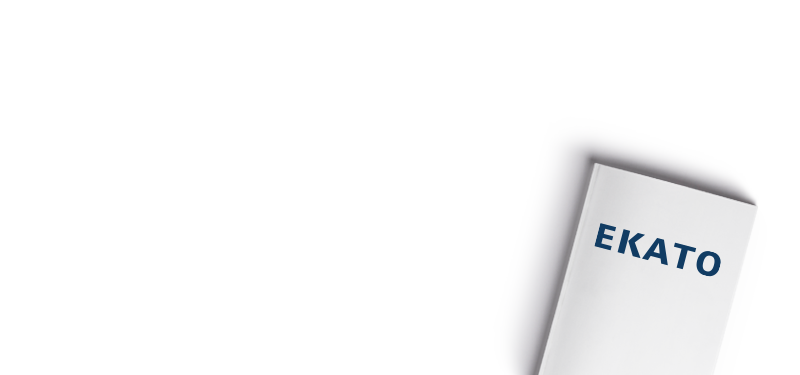