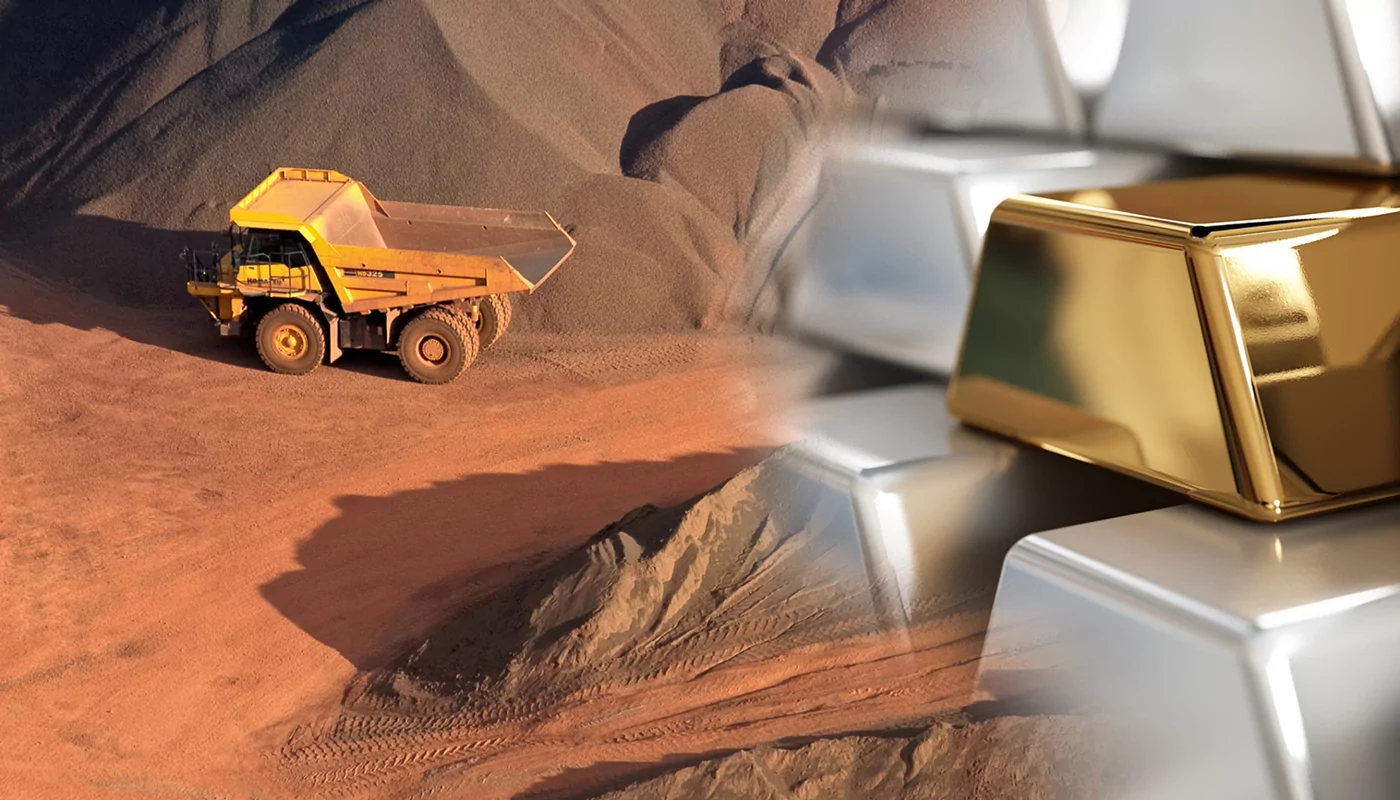
湿法冶金搅拌混合技术
采用湿法冶金工艺提取金属
EKATO 在湿法冶金行业
在湿法冶金中,三种主要的搅拌器类型是高压釜、常压罐和浸出罐搅拌器。EKATO是热压釜搅拌器的全球市场领先者之一。公司能够利用其丰富的经验提供定制的解决方案。公司提供广泛的服务,包括实验室测试,CFD和FEA研究,搅拌机的设计和制造,以及现场服务。EKATO定期设立加气常压储罐的新标准。
EKATO系统与市场上其他技术相比具有以下优势:
- 固体悬浮液的高传质率和高循环率意味着湿法冶金工艺的高收率和更好的结果。
- 更高的加气量有助于显著节省成本。
- 即使在曝气量非常高的情况下,运行稳定,运行成本更低。
湿法冶金中的高压釜和罐搅拌机
高压釜搅拌机
EKATO是高压釜搅拌技术的世界领先者。EKATO提供定制的解决方案,并在全球范围内的高压釜应用领域拥有宝贵的经验。我们的服务范围广泛,包括实验室测试、CFD和FEA研究、搅拌机的设计和制造以及现场协助。
EKATO提供强大的机械设计和高质量的制造(焊接钛洁净车间)。通过我们的密封部门,我们为高压釜提供完整的机械密封解决方案和密封支持系统。当传统的常压浸出法提取不经济时,采用高压釜技术进行湿法冶金。
高压反应釜是典型的水平容器,分为3至9个隔间或一系列单个级联容器,在高温高压下工作。极端温度和波动的压力状态需要良好的设计和最好质量的产品,以确保最大的可用性和寿命。
常压加气罐搅拌器
在连续常压操作条件下的搅拌釜反应器实现了许多气体湿法冶金浸出工艺的重要关键功能,例如
- 生物浸出反应器
- 直接浸出
- 预氧化槽
- 氰化物解毒
- 除砷
- 铁沉淀
- 充气氯化物浸出,例如 用于哑光镍处理
- 钪和稀土元素的回收(使用 SO2 气体)
- 生产电池级碳酸锂(含CO2气体)
除了实现“规模经济”和提高工艺性能外,实现此类系统的成本优化是一个基本目标。 因此 EKATO 开发了专有和独特的加气解决方案 EKATO COMBIJET 和 EKATO COMBIJET PLUS。
大型罐和浸出罐搅拌机
由于矿体的质量通常会随着丰富资源的枯竭而下降,因此一种趋势是在一个工厂或模块中处理更多的矿浆量,这导致当前和未来项目的容器尺寸进一步增加。 这些单元必须设计可靠,以确保整个工厂能够可靠运行。 混合任务可以是从固体悬浮任务到非牛顿浆料的苛刻混合,例如,如果必须处理增加的固体浓度。
典型应用是
- 浸出罐 (CIL, CIP)
- 非牛顿浆料与增加的固体浓度的混合,如高压釜进料罐和浆料管道用罐
- 回收/调节槽,例如CCD级间混合器,过滤加料槽,…
- 储罐和缓冲罐
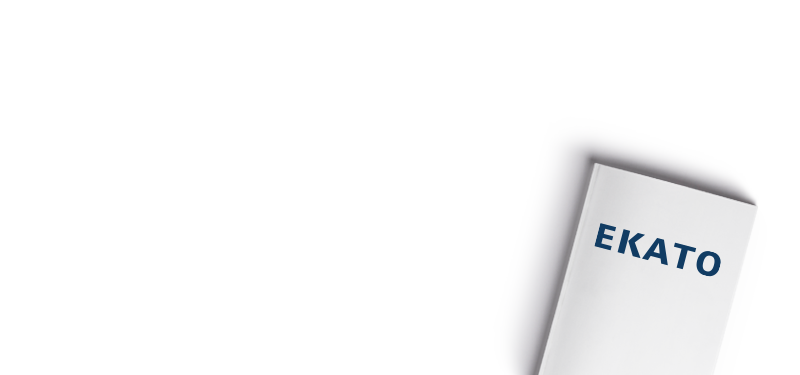