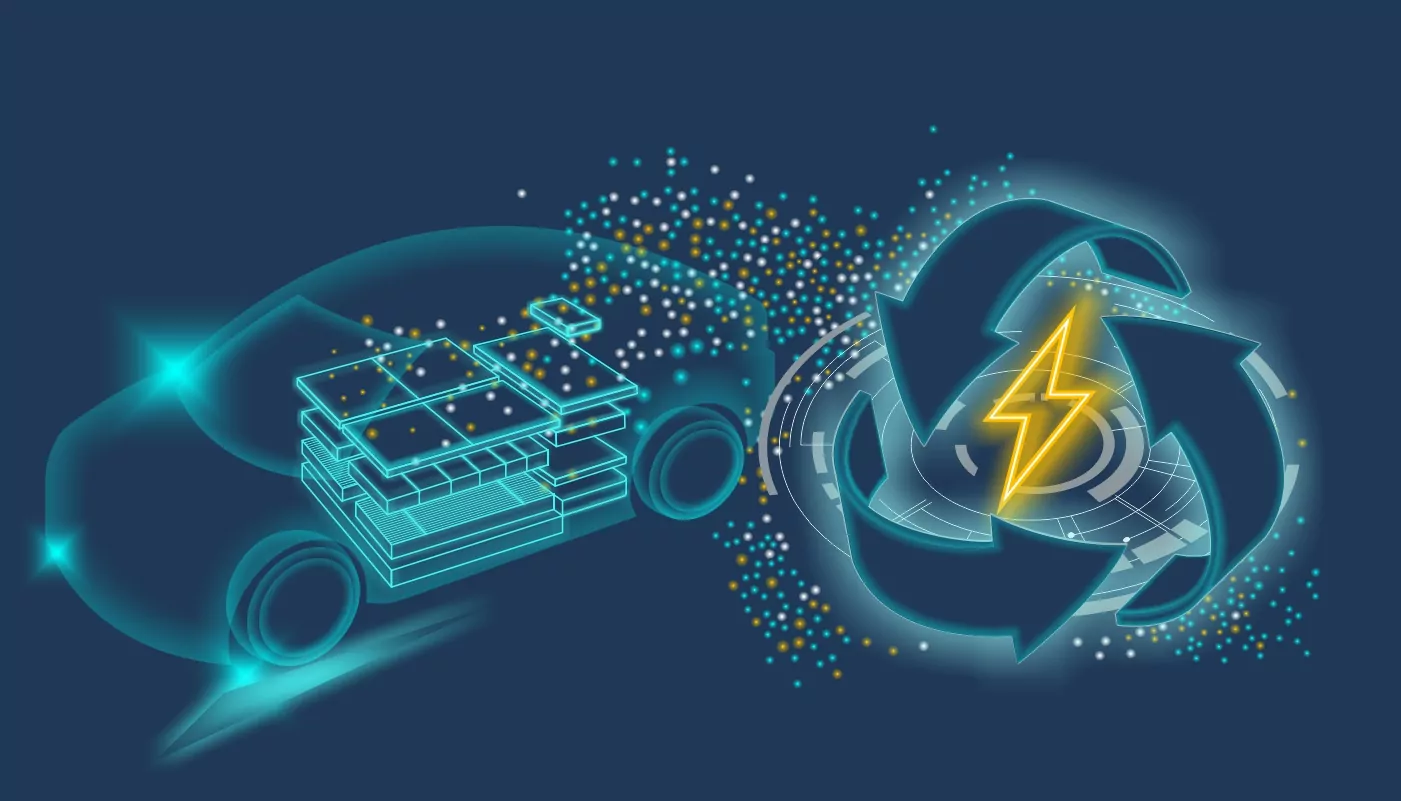
Battery Recycling
Innovative Process Solutions for Battery Recycling and Hydrometallurgy

EKATO Group, through its specialized divisions EKATO SYSTEMS and EKATO Minerals Processing, delivers industry-leading solutions for sustainable battery material recovery and precious metal extraction. Our comprehensive technology portfolio encompasses:
Core Competencies:
- Advanced vacuum contact drying systems for battery scrap processing
- Proprietary electrolyte recovery technology for shredded batteries
- Specialized black mass electrolyte extraction processes
- State-of-the-art hydrometallurgical reactor systems
- High-efficiency mixing solutions for critical metal recovery (Li, Ni, Mn, Co)
With decades of process engineering expertise, we optimize resource recovery while minimizing environmental impact through our patent-free system solutions. Our proven technology platforms ensure precise process control and maximum operational reliability across the entire battery recycling value chain.
Technical Specifications: Our systems feature dual-mode process control with optimized parameters:
Partner with EKATO to transform your battery recycling operations and advance sustainable materials recovery for the circular economy.
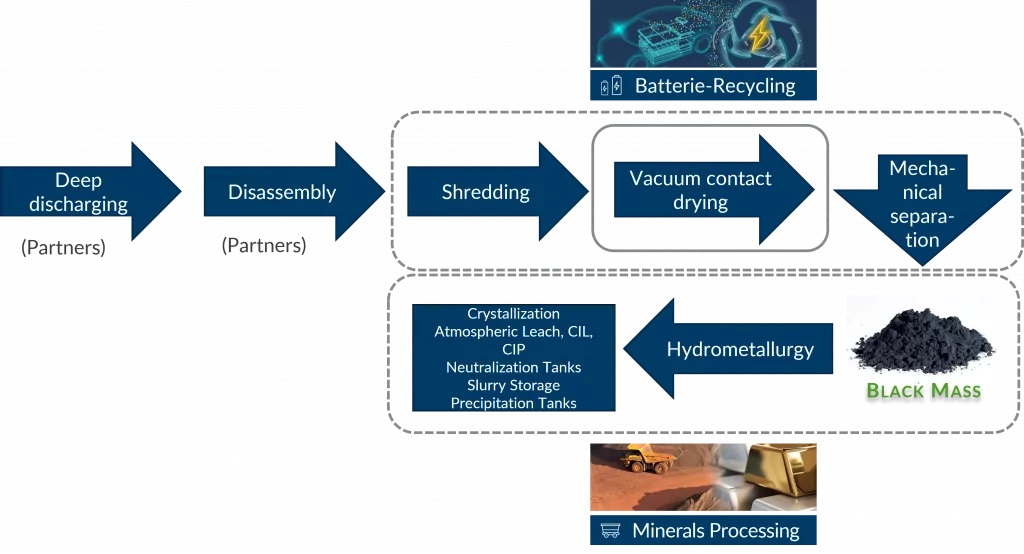
EKATO SOLIDMIX Applications in Battery Material Production and Battery Recycling
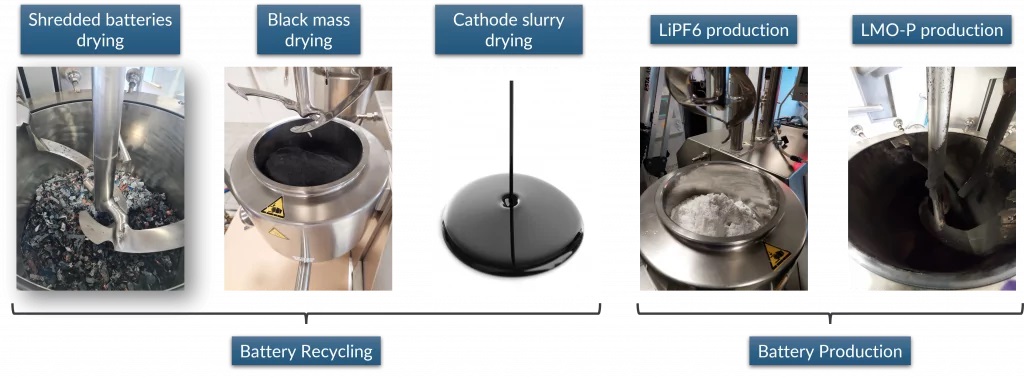
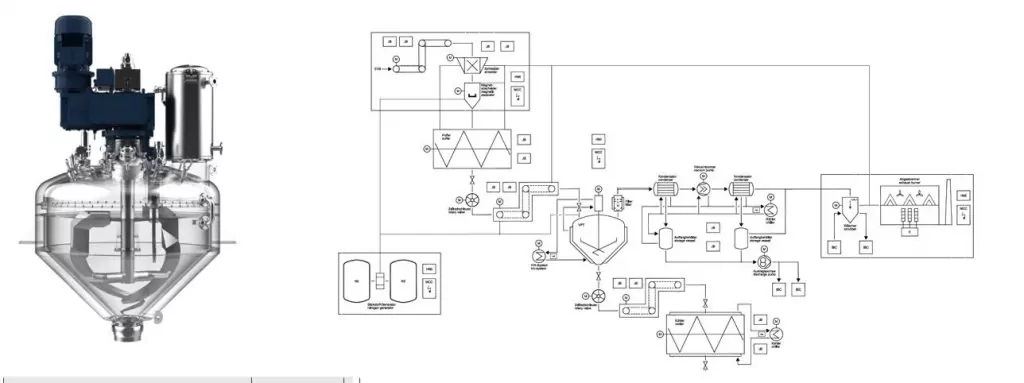
EKATO SOLIDMIX
EKATO builds the systems “technically tight” and thus minimizes the strain on the environment and the operator. The environment is not exposed to the solvents – this simplifies any explosion protection measures of the downstream equipment.
The HF resistant EKATO Solvent Recovery System (SRS) allows highest recovery rates of the typical electrolytes in the recycling industry – adding to your recovery rate balance. In the EKATO pilot plant, the drying process can be reproduced on a small scale. The focus here is on optimizing the processes.
Solvent residues that cannot be separated (VOC) are processed in a downstream exhaust gas treatment system. The EKATO dryer has a highly efficient solvent recovery system. This means that the downstream exhaust gas treatment system can be very cost-effective.
The EKATO drying process removes the common solvents in battery scrap or black mass (water, EC, EMC, DMC). The drying principle works on purely physical principles (temperature, pressure, time and shear). This means that the EKATO drying system can dry any solvent that follows these basic physical principles. With the EKATO drying system you are flexible and equipped for the future.
Black mass drying
Black mass drying is crucial for reducing solvent content, which is essential for efficient black mass processing. This reduction enhances the material’s value, optimizing subsequent recycling and resource recovery.
EKATO SOLIDMIX features:
EKATO builds the systems “technically tight” and thus minimizes the strain on the environment and the operator. The environment is not exposed to the solvents – this simplifies any explosion protection measures.
The HF resistant EKATO Solvent Recovery System (SRS) allows highest recovery rates of the typical electrolytes in the recycling industry – adding to your recovery rate balance. In the EKATO pilot plant, the drying process can be reproduced on a small scale. The focus here is on optimizing the processes.
Solvent residues that cannot be separated (VOC) are processed in a downstream exhaust gas treatment system. The EKATO dryer has a highly efficient solvent recovery system. This means that the downstream exhaust gas treatment system can be very cost-effective.
The EKATO drying process removes the common solvents in black mass (water, EC, EMC, DMC). The drying principle works on purely physical principles (temperature, pressure, time and shear). This means that the EKATO drying system can dry any solvent that follows these basic physical principles. With the EKATO drying system you are flexible and equipped for the future.
Black mass can be dried cost-effectively to a low moisture content. This significantly increases the resale value. The absence of organic solvents in the black mass is essential for further processes in hydrometallurgical processing.
Cathode / Anode slurry drying
Cathode and anode slurry drying is crucial when mechanical dewatering reaches its limits. Vacuum contact drying is the optimal choice, achieving minimal moisture levels and maximizing yield. Our equipment is designed to minimize product loss, featuring a single-pot design that seamlessly transitions from slurry preparation to vacuum drying, ensuring efficiency and high-quality output in battery recycling processes.
EKATO SOLIDMIX features:
Before thermal drying, the slurry should be pre-dried by means of mechanical dewatering. This is often not possible. The EKATO Vacuum dryer can also be used to pre-evaporate the slurry (Fed Batch Process). The evaporated solids cake is finally dried in the same apparatus in a deep vacuum to the final moisture content.
EKATO builds the systems “technically tight” and thus minimizes the strain on the environment and the operator. The environment is not exposed to the solvents – this simplifies any explosion protection measures.
The EKATO drying process removes the common solvents. The drying principle works on purely physical principles (temperature, pressure, time and shear). This means that the EKATO drying system can dry any solvent that follows these basic physical principles. With the EKATO drying system you are flexible and equipped for the future.
In the technical design of the EKATO SOLIMIX dryers, great importance is attached to maximum yield and a hydrofoil agitator design with minimum wetted surfaces.
To minimize iron contamination, EKATO SOLIDMIX dryers operate at low speeds and are also available in stainless steel and non-ferrous materials.
LiPF6 production
LiPF6 moisture removal and drying are optimized with our twin dryer design, ensuring continuous operation and accommodating large capacities. Our system provides effective process control, managing temperature and pressure for maximum flexibility to adapt to product changes. This ensures efficient and reliable drying, crucial for maintaining the quality and performance of LiPF6 production in battery grade.
EKATO SOLIDMIX features:
EKATO builds the systems “technically tight” and thus minimizes the strain on the environment and the operator. The environment is not exposed to the dust and solvents – this simplifies any explosion protection measures.
The EKATO drying process removes the common solvents. The drying principle works on purely physical principles (temperature, pressure, time and shear). This means that the EKATO drying system can dry any solvent that follows these basic physical principles. With the EKATO drying system you are flexible and equipped for the future.
Batch dryers with a nominal volume of up to 32 m³ are available . A twin arrangement forms a continuous drying system.
LiPDF6 can be dried cost-effectively to a moisture content of less than 500 ppm. This simplifies the handling in the downstream process.
The EKATO SOLIDMIX dryers are designed for the harsh operating conditions in the mining and mineral processing sector. Even in remote locations.
Lithium Carbonate Production
Li2CO3 moisture removal and drying are optimized with our twin dryer design, ensuring continuous operation, and accommodating large capacities. Our system provides effective process control, managing temperature and pressure for maximum flexibility to adapt to product changes. This ensures efficient and reliable drying, crucial for maintaining the quality and performance of Lithium Carbonate production in battery grade.
EKATO SOLIDMIX features:
EKATO builds the systems “technically tight” and thus minimizes the strain on the environment and the operator. The environment is not exposed to the solvents – this simplifies any explosion protection measures.
The EKATO drying process removes the common solvents. The drying principle works on purely physical principles (temperature, pressure, time and shear). This means that the EKATO drying system can dry any solvent that follows these basic physical principles. With the EKATO drying system you are flexible and equipped for the future.
With the EKATO dryer technology, Li2CO3 can be produced with a purity of 99.5%. This corresponds to the standard battery quality. The drying process allows low residual moisture levels of 0.4% and below. The EKATO SOLIDMIX dryers are designed for the harsh operating conditions in the mining and mineral processing sector. Even in remote locations.
Batch dryers with a nominal volume of up to 32 m³ are available. A twin arrangement forms a continuous drying system.
LMO-P Production (LiMn2O4 (LMO-P cathode)
With over 30 years of experience in solids handling and drying, EKATO leads the way in LMO-P battery material development and production. Our innovative technologies pave the path to the future, breaking new ground in battery manufacturing. Trust EKATO’s expertise to deliver advanced solutions, ensuring high-quality production and efficient processes in the evolving energy landscape.
EKATO SOLIDMIX features:
EKATO builds the systems “technically tight” and thus minimizes the strain on the environment and the operator. The environment is not exposed to the solvents – this simplifies any explosion protection measures.
The EKATO drying process removes the common solvents. The drying principle works on purely physical principles (temperature, pressure, time and shear). This means that the EKATO drying system can dry any solvent that follows these basic physical principles. With the EKATO drying system you are flexible and equipped for the future.
The EKATO SOLIDMIX dryers are prepared for LMO-P processes due to their flexibility in application.
EKATO SYSTEMS laboratory for battery materials / black mass testing
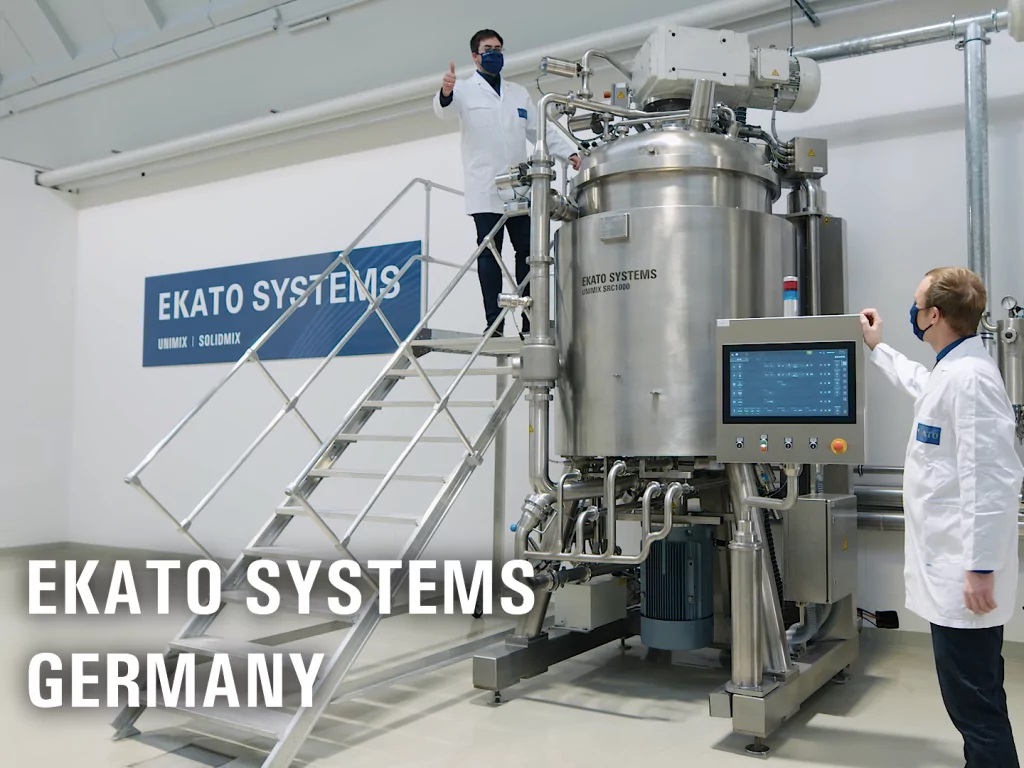
EKATO mixing solutions in the hydrometallurgical treatment of Black Ma
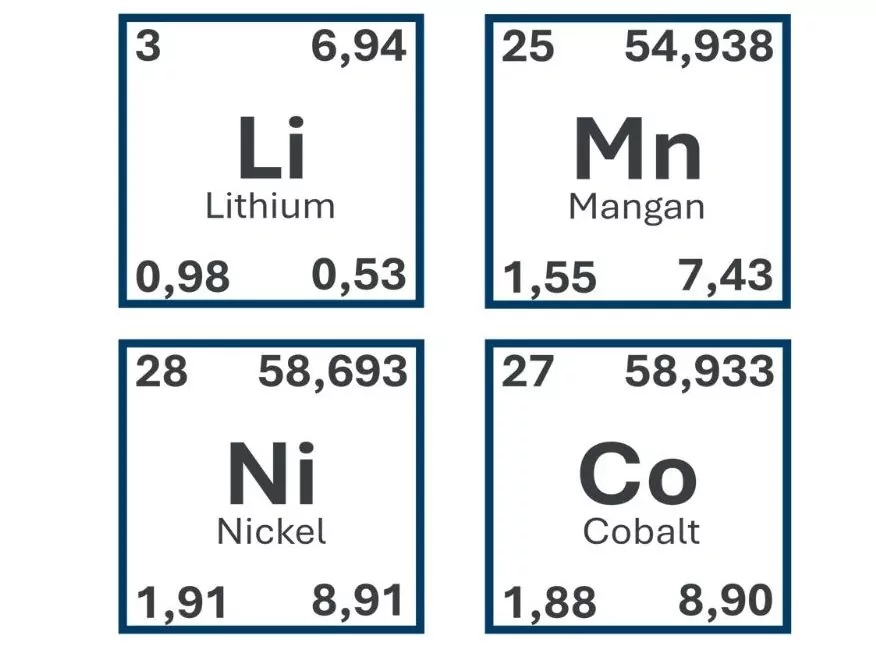
Pressure Oxidation Autoclaves (POX)
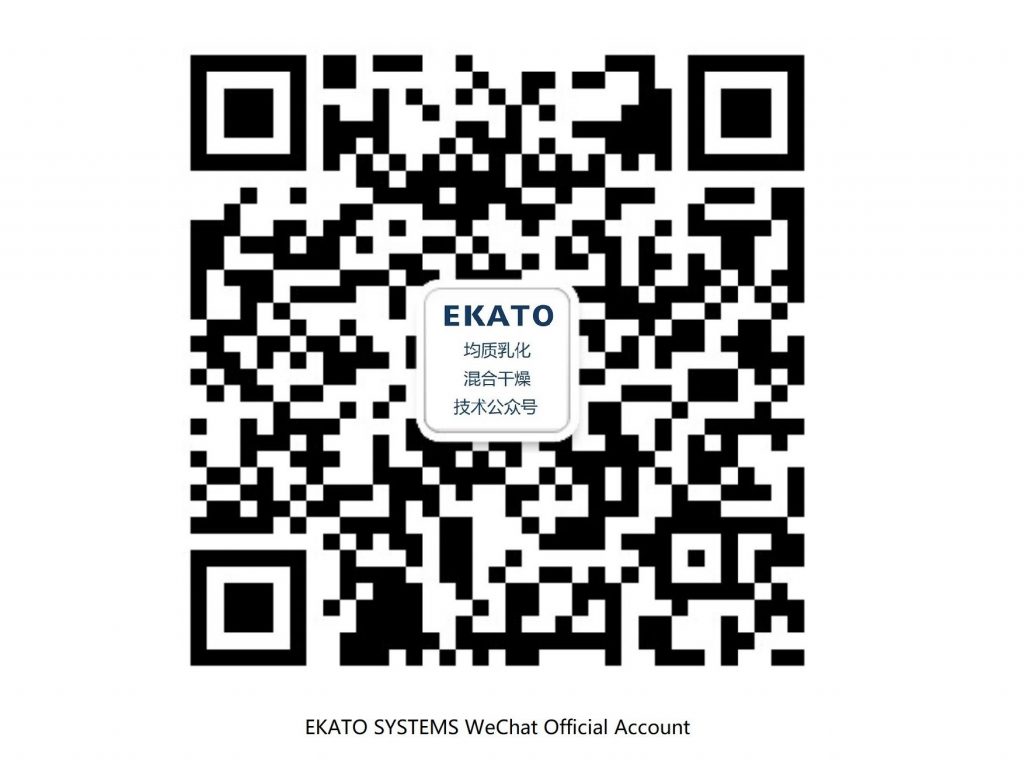