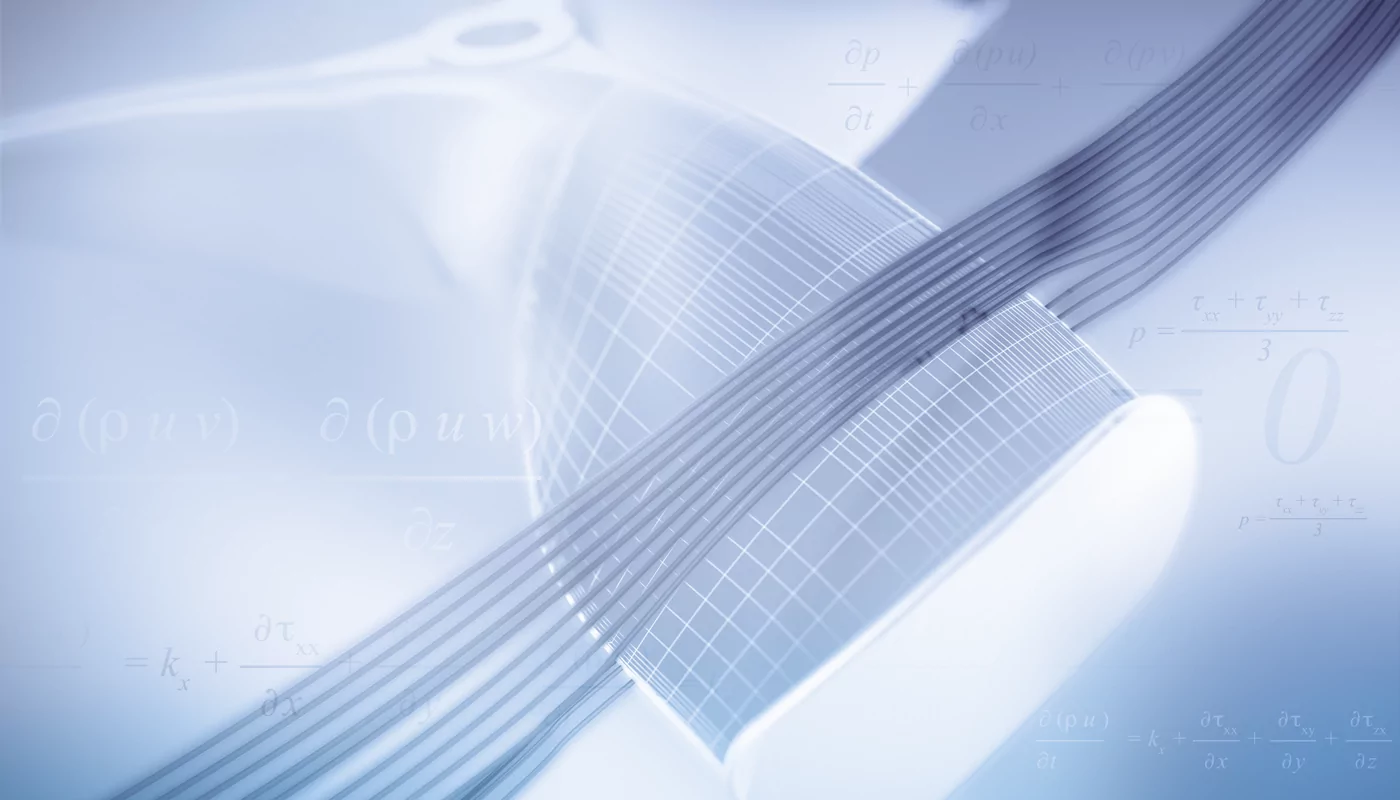
Process Development
Developing the Optimal Mixing Solutions of Tomorrow
Research and Development Centers
EKATO operates its two state-of-the-art research and development centers at its headquarters in Schopfheim (Germany).
EKATO – Research and Development For innovative mixing process solutions
R&D Center EKATO RMT
The R&D center of EKATO RMT focuses on the development and optimization of all liquid-based mixing systems:
- Homogenizing (miscible liquids from turbulent to highly viscous)
- Gas-liquid (dispersion)
- Solid-liquid (suspension)
- Liquid-liquid (disperssion)
- Heat transfer (heat supply or heat dissipation in the mixing system)
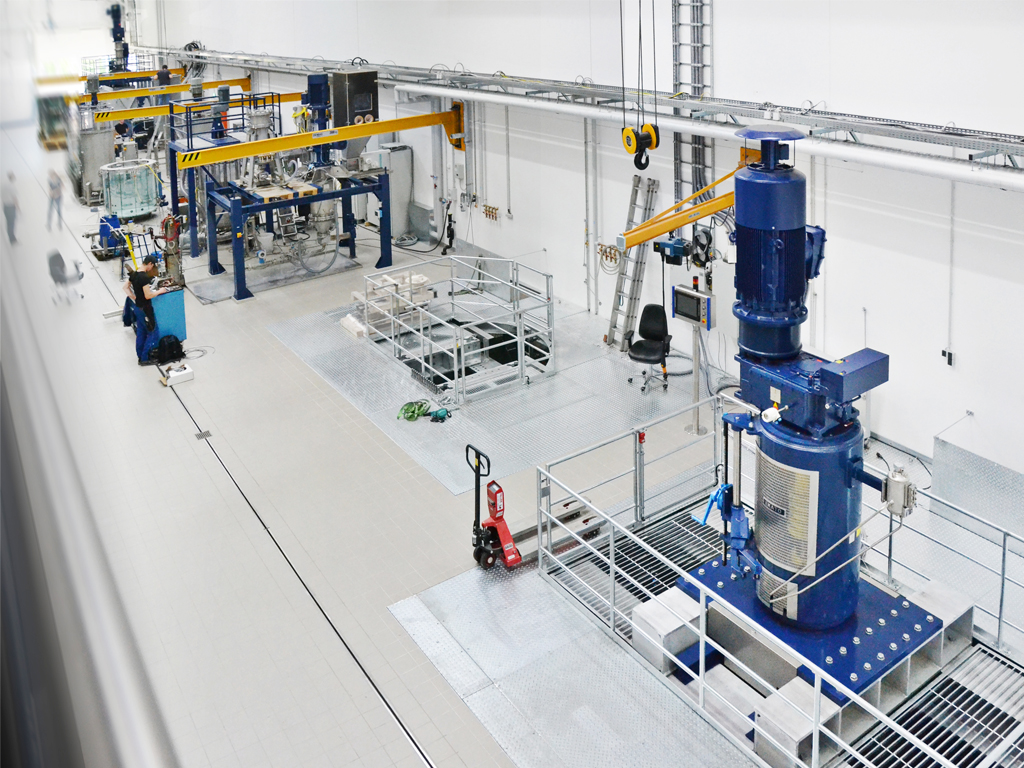
R&D Center EKATO SYSTEMS
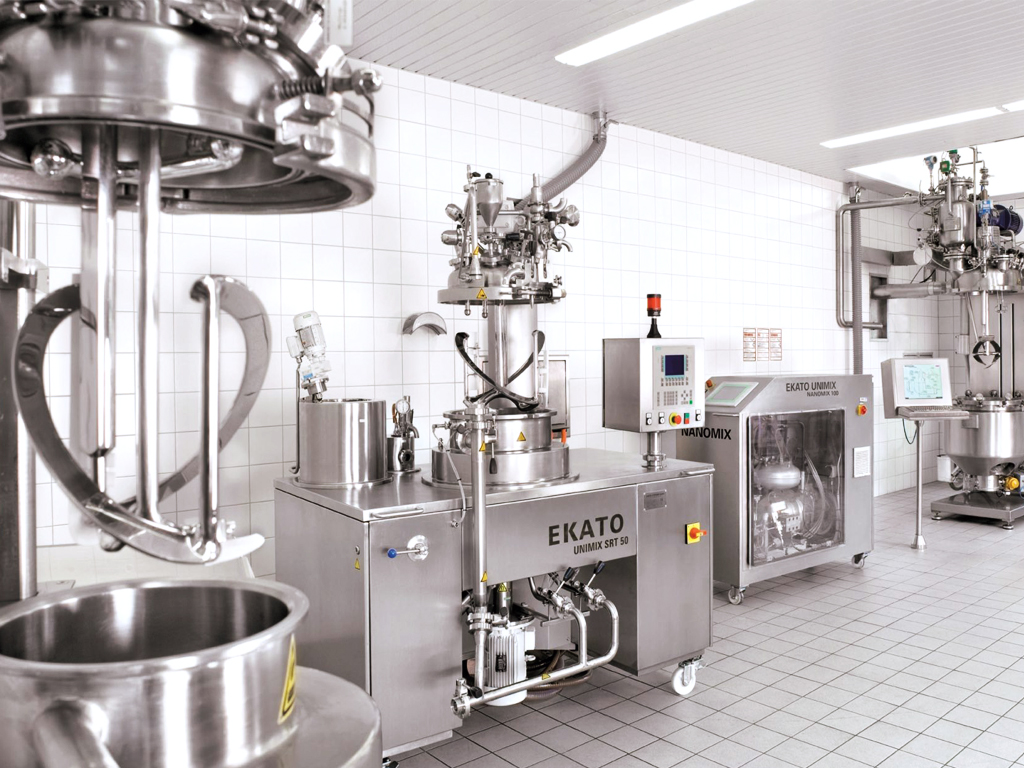
Analytical Measuring Instruments:
- Beckmann Coulter LS 13320 - laser diffraction particle size analysis
- Anton Paar MCR 52 – rheometer
- Brookfield DV-II+ – viscometer
- Sartorius MA40 – infrared balance to determine the residual moisture
- Transmitted light microscope
- Ring shear cell – to determine e.g. friction angles for bulk solids
Our customers have the possibility to attend tests directly on site at EKATO or to follow them in a live stream with the help of our WebLab. EKATO offers its customers the greatest possible flexibility with these centers for the development or optimization of their specific processes. In addition, we offer our customers the option of renting mobile laboratory equipment to carry out tests at their own sites.
EKATO WebLab Every successful project begins with trials in the EKATO R&D laboratory. Live from anywhere in the world!
Process Development / Optimization with EKATO
EKATO consults and accompanies its customers throughout their entire customer journey. Starting with the initial idea, through possible trials and subsequent scale-up into the industrial mixing process, to the actual mixing system - or even to the turnkey process plant. Our experts advise and support you in all development steps:
- Analysis of available data
- Carrying out tests
- Creation of flow simulations (CFD)
- Evaluation of test and simulation results
- Development of new impellers / mixing systems
- Safe scale-up to production scale
- Conceptual design and construction of the optimal mixing system / reactor including periphery up to a turnkey plant
Process expertise from EKATO
Every development with EKATO is based on decades of expertise in the physical and chemical fundamentals of mixing processes and procedures. Only an understanding of the relationships between the mixing process and the process result leads to an optimal solution.
On the one hand, the focus is on the mixing systems themselves. Thanks to the latest methods of flow simulation, impellers can be optimized to meet process-specific requirements, whether it is a matter of generating or minimizing shear stress, maximizing mixing efficiency and heat transfer at different viscosities, or reducing wear.
A strongly noticeable trend in the process industry is the switch from a batch process to a continuous mode of operation. EKATO, with its team of chemical and process engineers, supports its customers in this process. With an optimized mixing system, any process can be operated more economically.
Flow simulations with CFD
With computational fluid dynamics (CFD), it is possible to gain precise insights into the fluid dynamics at the impellers and vessel internals, as well as over the entire reactor. The major advantage is that these simulations can be used to visualize flow conditions on an operational scale. Therefore, these simulations at EKATO are a very good completion to the test programs and scale-up models which are based on them.
Flow-optimized impellers can meet process requirements more efficiently – for example, with minimum power inputs. For the design of the mixing process, it is of great importance, to know the velocity distribution of the flow in the stirred vessel, so that potential zones of low mixing intensity can be identified and eliminated by suitable adaptation of the stirring system. Additionally, the simulation results allow geometrical optimization of various internals in the vessel, such as feed pipes or heating / cooling coils.
Measured hydraulic loads caused by the inflow of such components allow EKATO to couple the simulation with the Finite Element Method (FEM), which significantly facilitates the evaluation of mechanical loads. As an additional side effect, these circumstances can be presented very clearly by appropriate visualization tools.
The use of new materials in mixing technology
The use of new materials – whether they are metallic, ceramic or in a composite – is being intensively evaluated in EKATO’s research and development centers and brought to market maturity. A longer service life of the agitator and the vessel internals reduce the plant owner’s operational and maintenance costs, especially in corrosive or abrasive environments. EKATO offers various types of coating to suit the requirements, from rubber coatings to hard coatings or even fully ceramic components.
The mixture makes the difference
The performance of research and development is based not least on well-coordinated teams with outstanding expertise in state-of-the-art technology. Our chemists, engineers and technicians develop solutions that guarantee plant operators the most efficient use of energy, raw materials and costs, as well as operational reliability.
Workshops and Seminars
In a diversified training and seminar concept, our experts from research and development, product management and sales regularly report on the latest developments and trends in mixing technology.
The offer ranges from specialized engineering days centrally at our headquarters in Germany, to events at selected locations worldwide – also in your area, to online seminars. Customized events or workshops for your company are also available by arrangement.
The EKATO seminar series includes
- Fundamental and state of the art knowledge of mixing technology
- Process applications in areas of: Hydrogenation, polymerization, crystallization, fermentation, photochemistry and many other agitation aspects and applications.
Our experts will be happy to come to your company with specially tailored workshops or hold them as online seminars. Talk to us about individual seminars for your company.