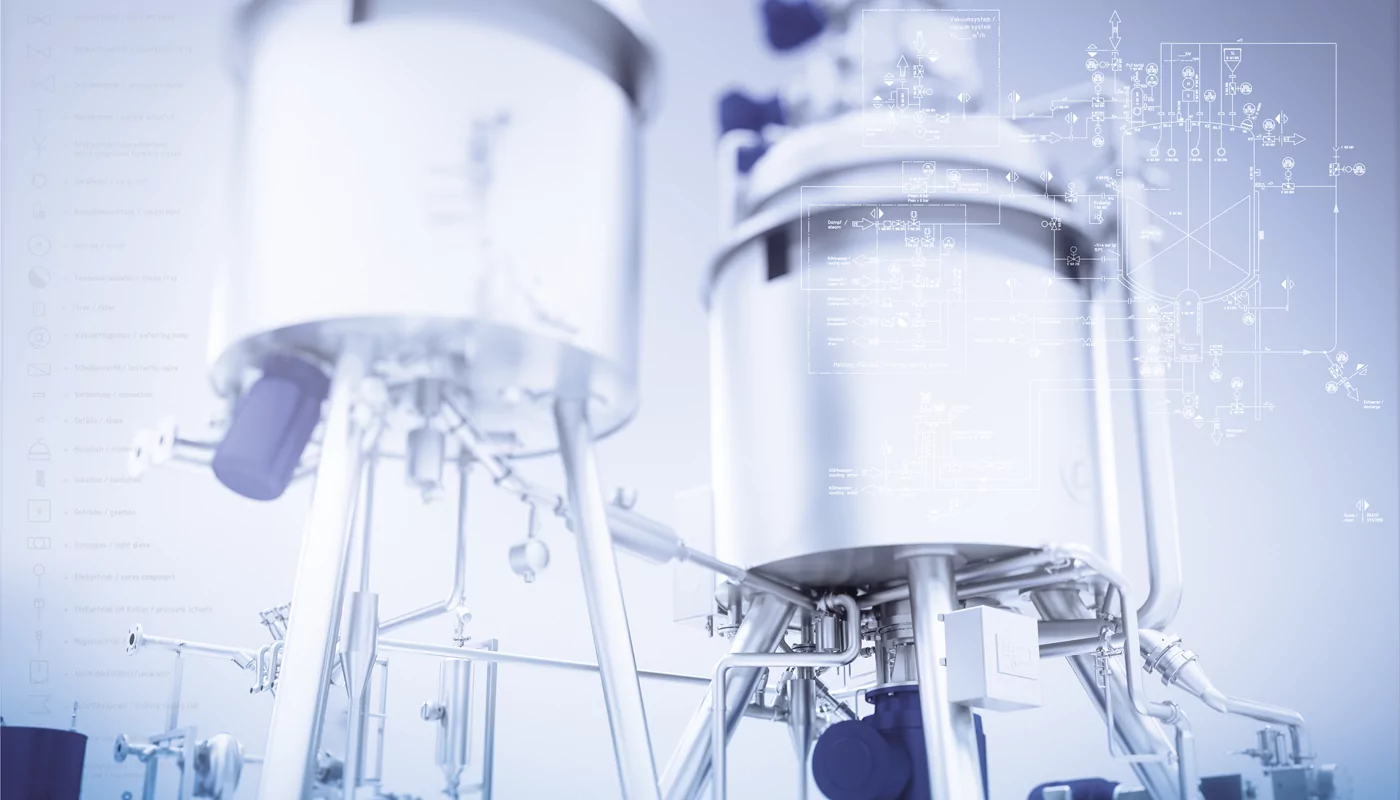
Engineering
Mechanically Safe, Robust and Reliable Design
The World's Most Powerful Agitators
In recent decades, there has been a massive trend in the process industry towards manufacturing larger plant units and to upscale equipment in order to achieve the benefits of “economies of scale”. Pursuing the “economies of scale” approach leads to cost advantages. As the size of equipment increases, the cost of production per unit of output decreases. This often goes hand in hand with the reduction of production lines and by means of process growth, i.e. higher productivity and yield. This can be observed particularly in the petrochemical, plastics and polymer industries, in hydrometallurgy or in industrial fermenters used in biotechnology. In some of these industries, reactor volumes have increased by a factor of ten since the 1990s.
EKATO is working closely with its customers to develop the next generation of industrial plants and, together with them, is developing the appropriate agitator technology solutions comprising agitators and the corresponding reactor designs.
What are the challenges of scaling?
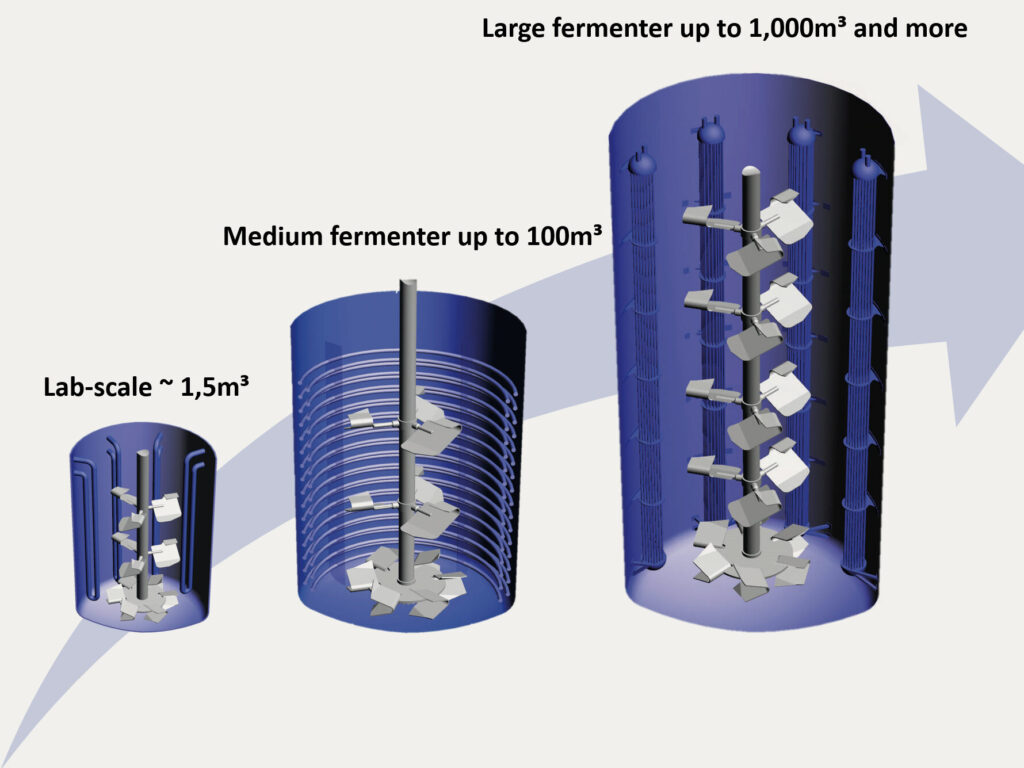
Finite Element Method (FEM)
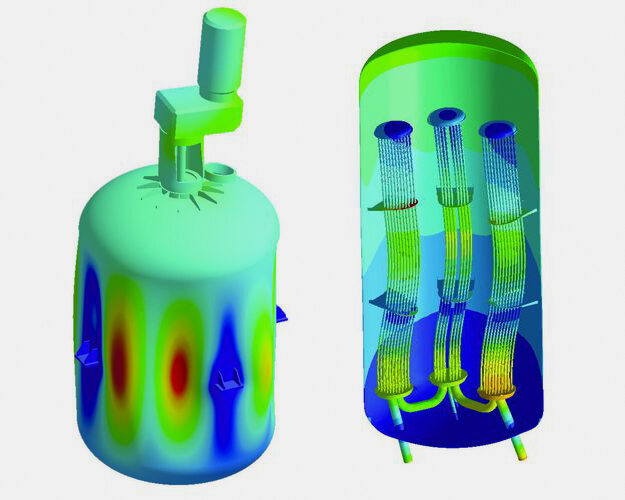
In accordance with its importance, the Finite Element Method (FEM) has now found its way into almost all conceivable physical disciplines. The most important methods in the field of mixing technology, which can be performed by EKATO, are:
- Structural mechanics calculations (operational stability, deformations)
- Modal / vibration analyses for the assessment of resonance hazards
- Thermal calculations
- Fluid-structure coupling (excitation frequencies, natural frequency, damping by fluid in the vessel)
In addition to the typically static loads caused by process pressure and temperature, stirred vessels and their internals are subject to high cyclic stresses generated by the agitator.
The most powerful agitators
Agitators with a drive power of up to 4,000 kW, agitator belt diameters of over 6 m or shaft diameters of over 500 mm are no rarity for EKATO. The total weight of such agitators often exceeds 100 tons. These dimensions lead to enormous static and dynamic loads. This requires an even more precise and reliable calculation of the forces acting on the entire vessel, its internals and supporting structure. EKATO can draw on decades of experience in this field, in which the calculation methods are constantly being further developed.
Stirred Reactors – from a Single Source
One challenge in the design of stirred reactors is the coordination of the interfaces between the agitator, vessel and its associated internals necessary for the process. Often, these individual components are supplied by different manufacturers, which can easily lead to coordination and information problems. For reasons of productivity and economy, it makes sense not only to adapt the agitator to a predefined vessel, but also to work out an optimum overall concept together with the plant operator and equipment manufacturer.
EKATO offers an extended engineering services and scope of supply, in order to guarantee the customers an efficient and smoot progress in the project with as few interfaces as possible. In addition to the agitators, we also take care of the associated process technology, such as heat exchangers, baffles, optimum positions of the feed and discharge pipes as well as vessel engineering – all from a single source.
Our project engineers coordinate the interfaces throughout the project, from manufacturing and pre-assembly to delivery, commissioning support and training.
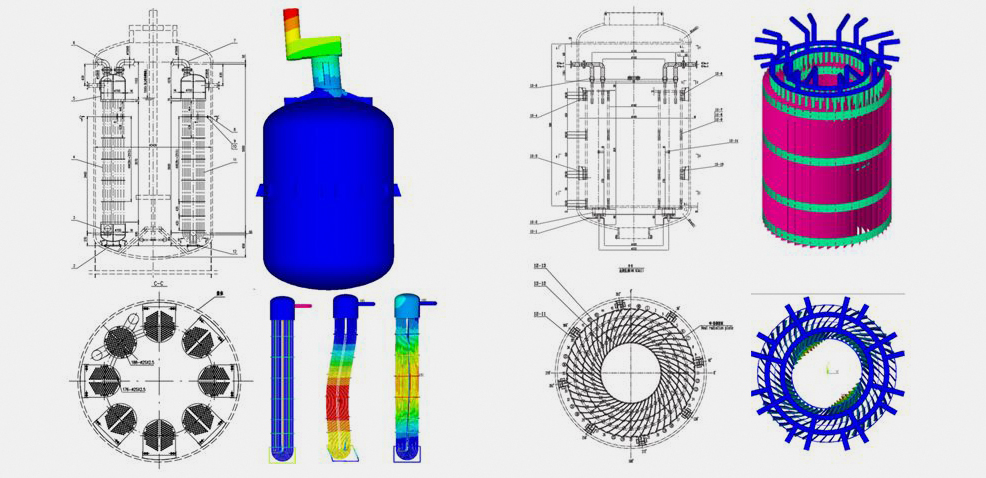
Process Plants / Units
The construction and design of complete process plants requires perfect interaction between the disciplines of process technology, automation and engineering. Based on key figures and process variables determined in feasibility studies and tests, plant components are designed using scientifically based scaling methods (scale-up), requirements are identified and combined to form a completely functional plant. The design of the plant or the components themselves also includes methods such as CFD analyses and FEM calculations in order to ensure plant functionality and safety. Automation plays a central role in the optimal interaction of the process plants. This combines the actuators and sensors of the plants according to the process requirements and customer needs. The degree of automation ranges from semi-automatic operation to fully automatic processes with recipe control, data recording and the documentation of the Batch (BatchRecord). Integrated plants are built for processes in the fields of SOLIDMIX and UNIMIX. SOLIDMIX covers the processes of solids drying and solids mixing, while UNIMIX offers solutions to produce suspension- or emulsion-based products in the low to high viscosity range. The range of process plants varies from pre-engineered solutions (short delivery times) for specific products of our customers to engineered solutions in which specific process and customer requirements are implemented.
Plant Design and Construction
In the Process Plants division, EKATO offers a comprehensive service and equipment package as a development and engineering partner for process plants based on stirred processes. With practical special knowledge and innovative methods from process and apparatus engineering, EKATO offers concept design, basic engineering, execution, procurement, and delivery as well as construction and commissioning of the system.
Concept Design
In the concept phase of the engineering, EKATO defines the essential process steps in the context of process analyses as well as mass and energy balances. If necessary, EKATO performs tests in its own highly corrosion-resistant laboratory and pilot apparatuses in which operating conditions up to 100 bar and 300°C are possible. The required scale-up to the operating scale is based on 80 years of expertise. The process concepts developed in this way are examined by our specialists regarding to feasibility, and an initial rough cost estimate is provided.
Basic Engineering
In the basic engineering phase, EKATO then technically and mechanically interprets the main apparatuses in interdisciplinary project teams and defines the utilities as well as the control and monitoring concept. An HAZOP is carried out together with the customer. Accompanied by further risk analysis, the P&ID and system layout will be gradually developed. With completion of the basic engineering, the system is then cost-assessed within a few percentage points.
Detail Engineering
In the detailing phase, the EKATO project team then specifies the equipment, fittings, and instruments in detail and clarifies their interfaces. On request, these will also be supplied by EKATO. In this case, EKATO takes over the entire order processing with technical, quality, and delivery schedule expediting at the component suppliers and manufacturers.
Installation and Commissioning
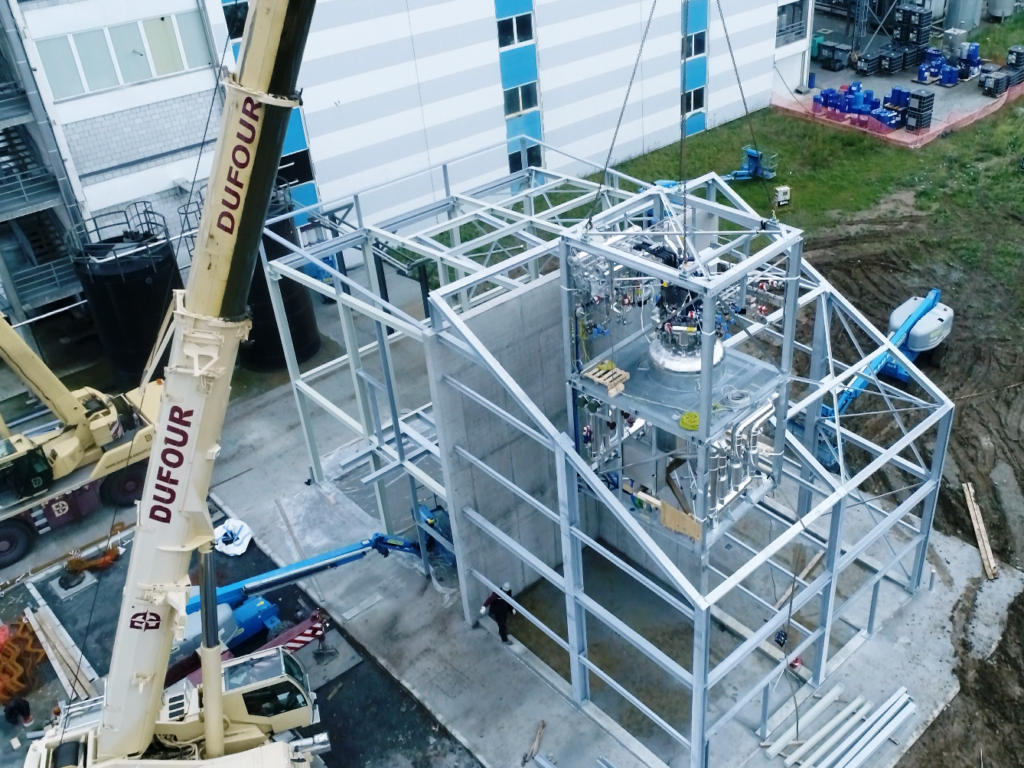
Summary
With this comprehensive range of services and equipment, EKATO offers partial or complete solutions from the idea to a technically and economically sound solution. By means of piloting and many years of experience in the scale-up of process engineering equipment, EKATO offers the customer process guarantees and provides high-quality production plants.