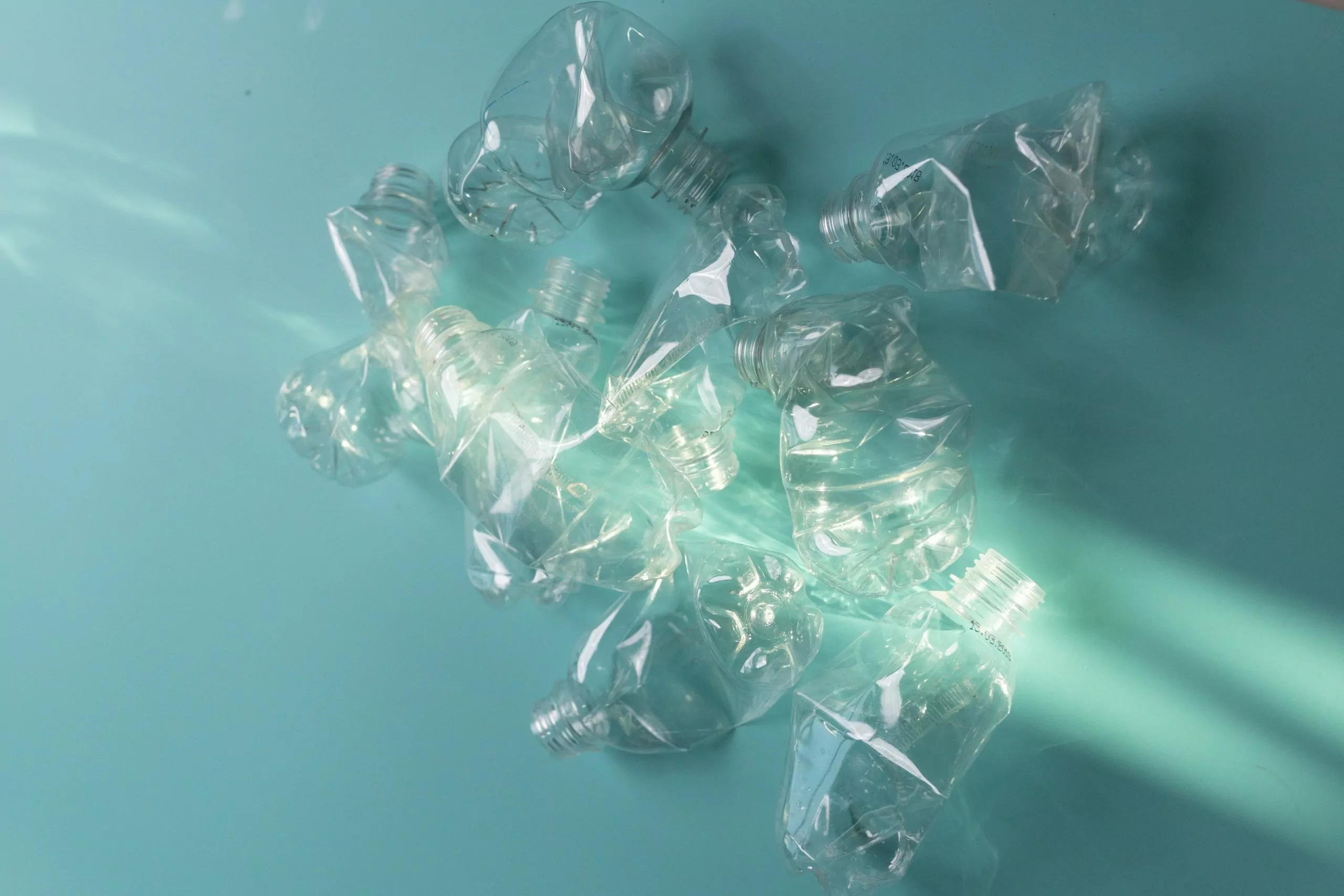
Chemical Recycling of Plastics
Chemical plastic recycling is becoming essential in the fight against the waste problem
The careless use of plastic has escalated into a worldwide environmental problem. Unfortunately, for the vast majority of polymer products, degradation in nature is either non-existent or extremely slow. This endangers the environment to an ever greater extent. The world’s oceans are particularly affected by the considerable quantities of plastic waste.
This is a global challenge! Therefore, the recycling of plastics is more and more in the focus of the general public. The goal should be a “Circular Economy”, ideally a worldwide closed loop of plastic products and plastic precursors.
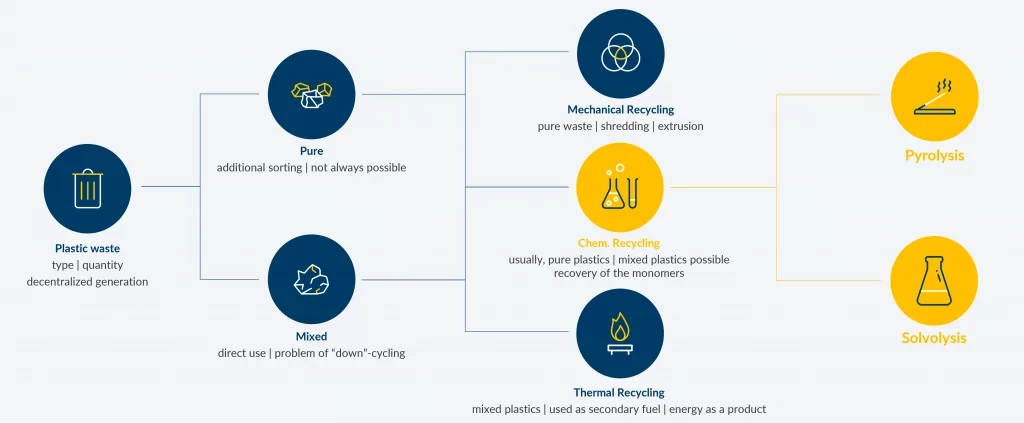
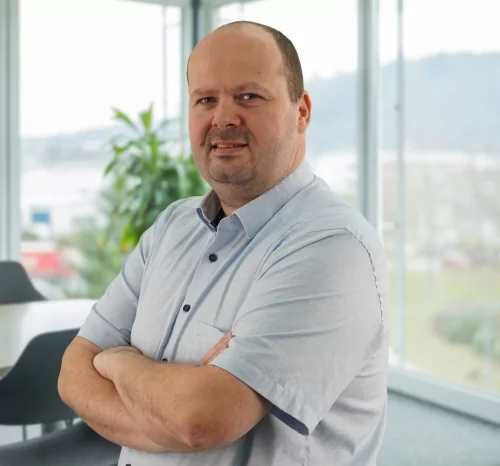
Process Consultation
Contact us today to connect directly with our Sales Project Manager and discover how we can enhance your process, equipment, and overall plant efficiency.
Chemical Recycling, the Next Step
Today, most recycling is done by mechanical processes. The very largest, widespread plastic waste fractions – for example, the contents of the “yellow bags” or the “yellow garbage cans” – contain many impurities, multilayer films, metals, dyes or additives. If these mixed fractions are to be successfully returned to a recycling loop, chemical plastic recycling processes must be established on a large scale in addition to mechanical ones.
Basic Process Challenges when Recycling Plastic
The input material must be prepared for a chemical recycling process in the first process step for dissolving or melting in such a way that trouble-free operation as well as a reproducible process result can be achieved. Because of the widely varying nature of plastic waste, this is where the first, major process challenge lies.
Not only the quality and “purity” of the input material usually vary greatly, but also central parameters such as bulk density, particle size distribution or even the wettability of the output material play a decisive role.
Depending on the process, there are usually very high viscosities or rheological challenges, such as flow limits. In these demanding media, not only the general mixing processes such as homogenization and suspension, but also the heat transfer must function reliably. If the initial mass is to be homogenized accordingly and brought to the required process temperature in the reactor, a well thought-out, sophisticated and efficient mixing technology concept is required.
Mixing Solutions Using the Example of EKATO PARAVISC
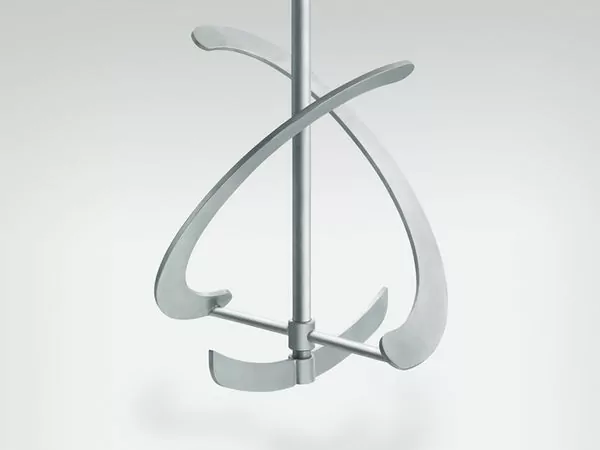
The axial mixing is achieved by the unique shape and arrangement of the EKATO PARAVISC’s two main blades. This impeller can be operated to convey both downward and upward, depending on the application. If it conveys downward, for example, the fluid is forced downward along the wall, changes its direction of movement at the bottom, and flows toward the surface in the area of the agitator shaft.
EKATO's Customized Reactor Concepts
For certain chemical recycling processes, such as thermal processes, some processes are already becoming established well beyond pilot scale.
Some solvent-based processes (solvolysis) as well as various catalyzed processes are already on their way from a pure, promising process idea to a pilot plant. EKATO offers tailor-made reactor concepts for this phase. On the basis of “Joint Development Agreements”, reactor concepts are developed from customer processes – which have already been appropriately tested in the laboratory – and implemented as scalable, modular pilot-scale plants.
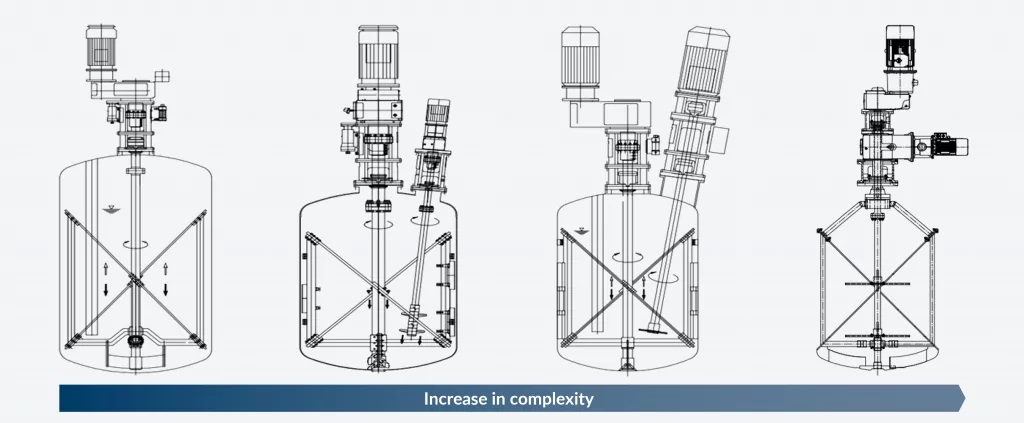
How EKATO can Support You
EKATO also supports innovative companies in the development of depolymerization technologies with its know-how and expertise in mixing and reactor technology.
In EKATO’s own technology center or in pilot plants tailored to the respective customer process, processes with different plastic wastes can be tested and optimized under realistic conditions on a technical scale. Based on the findings from pilot tests, EKATO develops a reactor system tailored to the customer’s needs.
EKATO also supports innovative companies in the development of depolymerization technologies with its know-how and expertise in mixing and reactor technology.
In EKATO’s own technology center or in pilot plants tailored to the respective customer process, processes with different plastic wastes can be tested and optimized under realistic conditions on a technical scale. Based on the findings from pilot tests, EKATO develops a reactor system tailored to the customer’s needs.
EKATO Capabilities
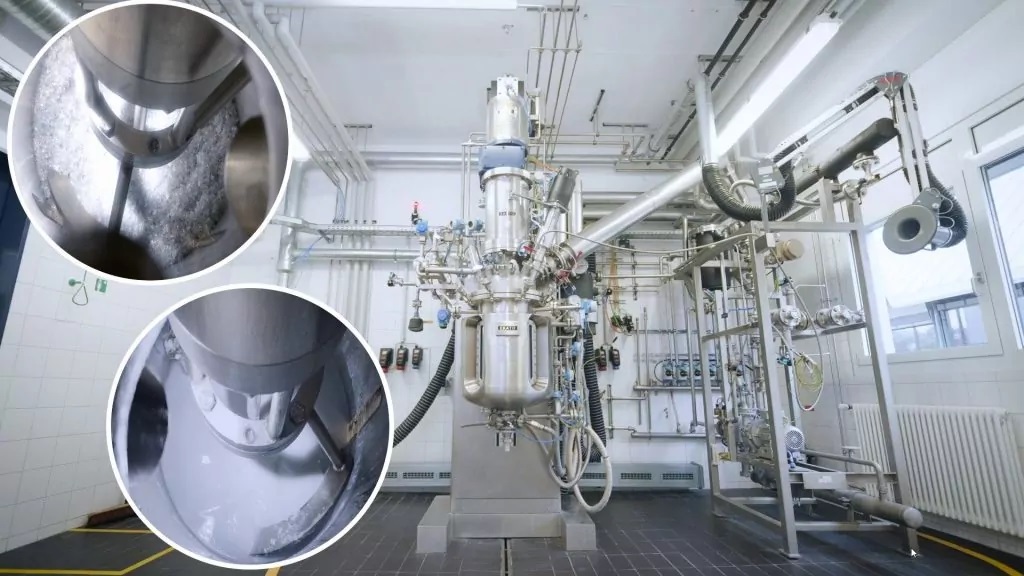