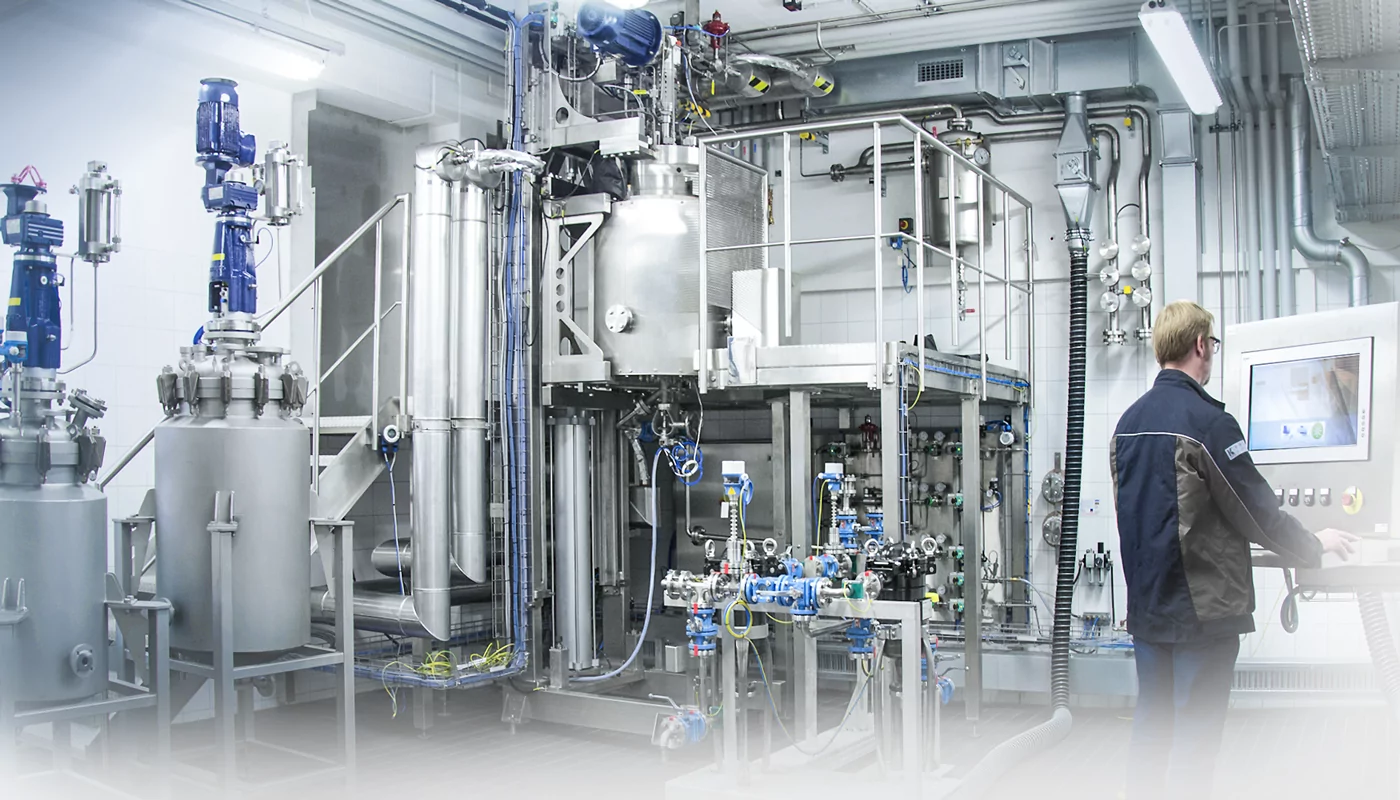
Hydrogenation Plants and Hydrogenation Reactors
Everything from One Source
Our hydrogenation portfolio includes:
- Consulting services
- Hydrogenation trials on EKATO rental equipment type ELA 5 at your plant
- Pilot scale hydrogenation trials (5 - 60 liters) at EKATO's hydrogenation pilot plant
- Conceptual and FEED studies
- Basic Engineering
- Detail Engineering
- Key equipment (EKATO hydrogenation reactors, catalyst preparation stations, catalyst filters, etc.)
EKATO designs and supplies hydrogenation plants for a wide range of industrial applications and industries:
- Flexible multi-product plants for the hydrogenation of pharmaceutical raw materials (API)
- Flexible multi-product plants for the hydrogenation of fine and specialty chemicals
- Plants for the hydrogenation of sugars to sugar alcohols
- Plants for the hydrogenation of fats, fatty acids and oils
- Plants for the continuous hydrogenation of basic chemicals
EKATO Hydrogenation Plants Tailored to your process
Modular Hydrogenation Plants
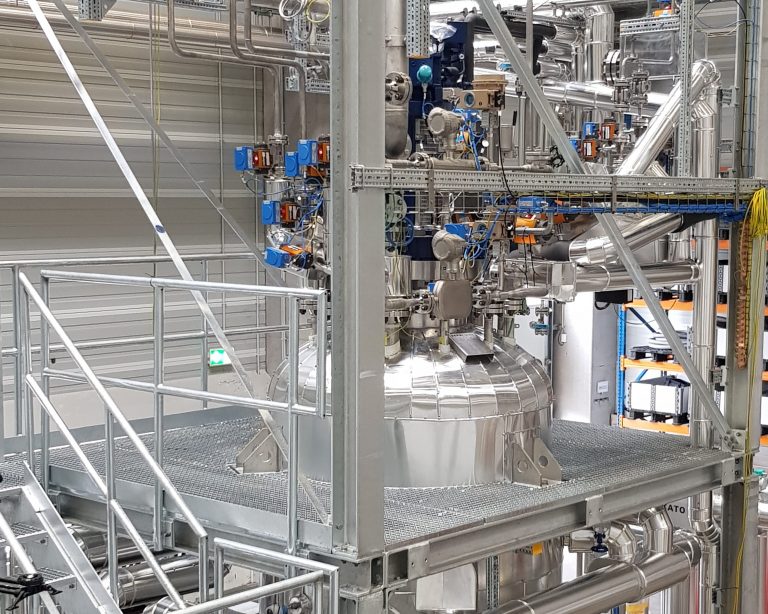
Modular hydrogenation plants from EKATO offer several advantages over conventional plants that are assembled on site. The main advantages of our modular plant technology are:
- One contact for everything: EKATO
- Shorter project lead times
- Lower total investment costs
- Very short interruption of the running production production, especially in case of plant extensions/conversions
- Precise and clean assembly of the plant in the modern large-capacity assembly halls at EKATO
- Safety test, function test and pre-commissioning commissioning including parameterization and configuration of the control system before delivery plant
A typical EKATO hydrogenation reactor module consists of:
- Steel structure of the hydrogenation reactor
- Piping and fittings
- Instrumentation
- Wiring and terminal boxes
- Insulation
- Control system (outside the skid)
EKATO Skid-mounted Hydrogenation Plants we ensure you a rapid market launch of your new chemical products, maximum efficiency and the greatest possible flexibility in production
The plant modules are generally assembled in EKATO’s own purpose-built assembly halls in Schopfheim or by selected certified subcontractors. Typical hydrogenation reactor modules from EKATO include reactor sizes from 50 l to 6000 l usable volume, 6 – 150 bar design pressure and can be made of various materials. Larger plants consist of more than one module and also include a catalyst preparation station, a catalyst filter, a heating / cooling station, and a flue gas scrubber.
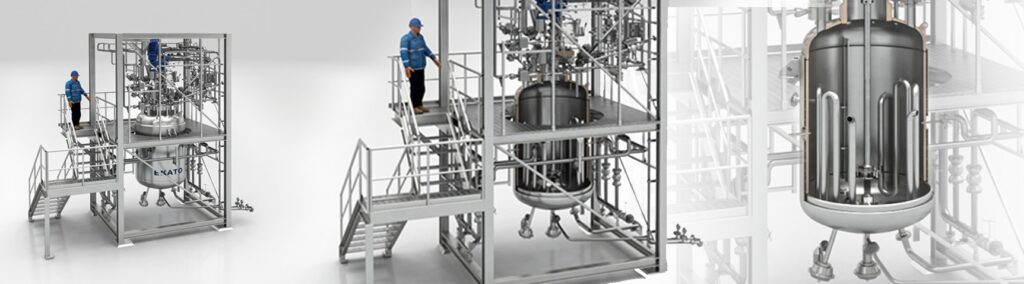
Hydrogenation Reactors
At the heart of each plant is the EKATO hydrogenation reactor, which is equipped with a special agitator called EKATO combined gassing system. EKATO combined gassing is used in more than 500 gas-liquid reactors worldwide and is an important basis for our success in numerous industrial hydrogenation applications.
EKATO GASJET in 30 m³ vessel – EKATO Product Applications: Recirculation of the non-reacted gas into the liquid phase
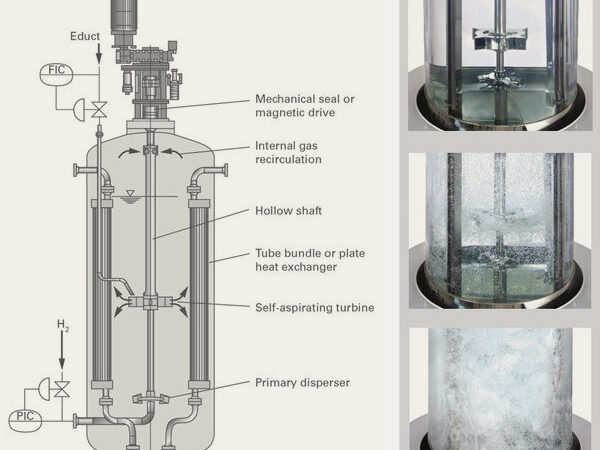
Advantages of the EKATO hydrogenation reactor:
- Compact design without external gas recirculation
- Two zones for gas dispersion (PHASEJET and GASJET)
- Optimum mass transfer and maximum availability of the dispersed gas
- No concentration or temperature gradient in the reaction phase
- High cooling capacity
- Different heat exchanger types available
- High mechanical reliability
- Available with mechanical seal or magnetic drive
- Available as batch or continuous reactor
- Simple, safe scale-up / scale-down
Technical data:
- Useful volume: 5 liters - 200 m3
- Design pressure: up to 220 bar
- Design temperature: 150 to 400°C
- Material: almost all metallic materials (carbon steel, stainless steels, Ni-based materials, titanium, etc.)
- Heat transfer vessel wall: double shell or half pipe coils
- Heat transfer internally: tube coils, tube bundle heat exchangers, plate heat exchangers
- Design always specially adapted to your needs
- Options: instrumentation, bottom outlet valve, discharge lances, sampling systems, bottom agitators, GMP design
Our services
EKATO combines the knowledge and experience for the integrated process and mechanical design of your hydrogenation reactor. Thus, we offer top performance for optimal technical and economic operation. Our services include:
- Reactor design considering stoichiometry and kinetics of your reaction
- Scale-up / scale-down
- Modeling and simulation
- Thermal balancing
- CFD-studies
- FEM-studies
Reliable and robust in operation
Due to the high volume-specific power inputs and the resulting high hydraulic load on vessel internals, the design of a hydrogenation reactor is particularly demanding. EKATO determines hydraulics-based parameters, such as the hydraulic loading of heat exchangers in the reactor, by numerical flow simulations (CFD). The information obtained from these simulations is indispensable for the static and dynamic dimensioning, as well as for the resonance-proof design of the hydrogenation reactor. The subsequent mechanical design of the reactor is also carried out in-house by EKATO using numerical methods such as FEA and CAE.
Modal Analysis of CoilsThe effect of excitation frequencies can be simulated by FEA. The results help to prevent fatigue failure by optimized design.
Flexible Hydrogenation Plant for Active Pharmaceutical Ingredrient Production (API)
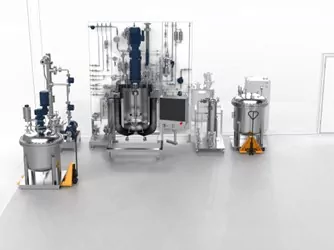
Your Advantages
- "Plug & Produce" Plant Concept
- Compact Modularity & Customizable Configuration
- Process Flexibility & Fast Campaign Changeovers
- Proven & Affordable Technology
- Enhanced Safety Concept
- All From A Single Source – EKATO
Trial Equipment & Piloting Process Development and Scale-Up
In our new Hydrogenation Test Center in Schopfheim, we can test and optimize your hydrogenation process with your original raw materials under realistic conditions on a technical scale. The aim is to obtain scalable test results for industrial plants with small product quantities. In this way, we guarantee you maximum security for your investment in the new construction or conversion of a hydrogenation plant.
For this purpose, we have hydrogenation reactors with filling volumes between 3 liters and 60 liters made of stainless steel and Hastelloy. We can perform hydrogenations at up to 100 bar and up to 250°C and also investigate the filtration behavior of the respective catalyst/product suspension.
Pilot Hydrogenation Plant HTC
Hydrogenation reactor and filtration unit
The EKATO HTC hydrogenation plant consists of a hydrogenation reactor with a filling volume of 60 l, a feed tank, a filtration unit and a filtrate tank. All vessels are equipped with a mixing system and are made of Hastelloy C22. With pressures up to 100 bar and temperatures up to 250°C, this offers a wide range of process engineering applications.
Characteristics
- Filling volume max. 60 liters
- Design temperature: 250°C
- Design pressure: 100 barg
- Installation in zone 1, IIC
- All wetted parts in Hastelloy C22 and Kalrez
- Exchangeable stirring systems
- Heating/cooling via wall and/or various internal heat exchangers
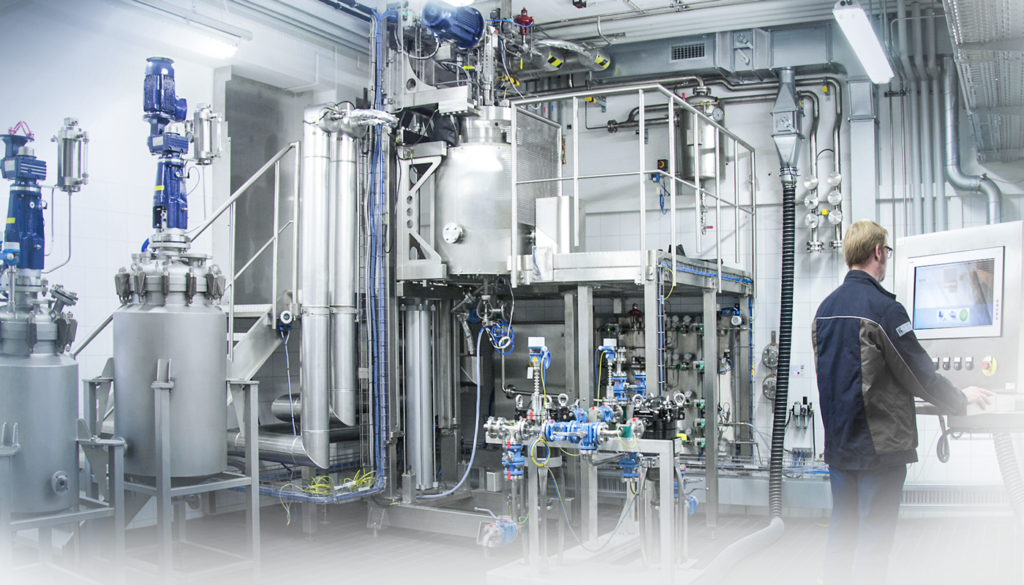
Area of application
This pilot plant is suitable for the investigation of a wide variety of hydrogenation processes such as:
- Grease hardening
- Sorbitol
- TDA
- Aniline
- Hydroxylamine
- Polymers
- Fine chemicals
Our service
Support by EKATO experts:
- Trial performance in EKATO laboratories
- Analytics (density, viscosity, GC, HPLC)
- Scale-up expertise
- Statement regarding process success
Laboratory Hydrogenation Plant ELA 5
Transportable laboratory unit for process development
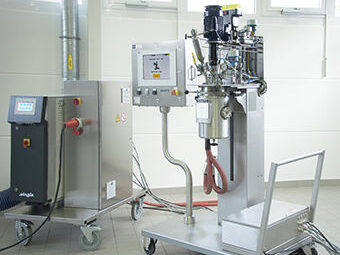
The EKATO laboratory hydrogenation plant can be rented from the following EKATO subsidiaries:
- EKATO Germany
- EKATO USA
- EKATO India
- EKATO Japan
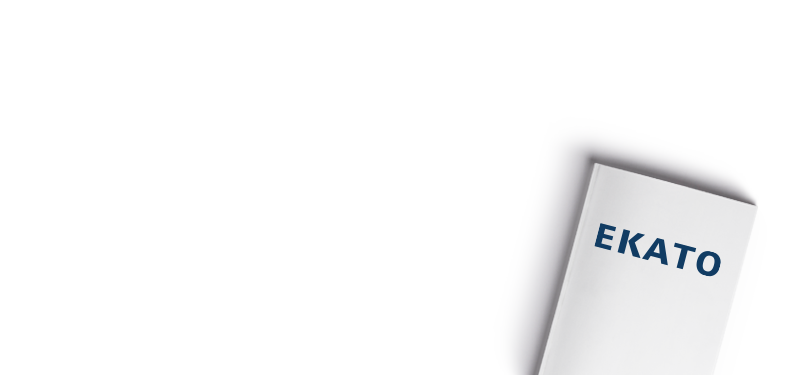