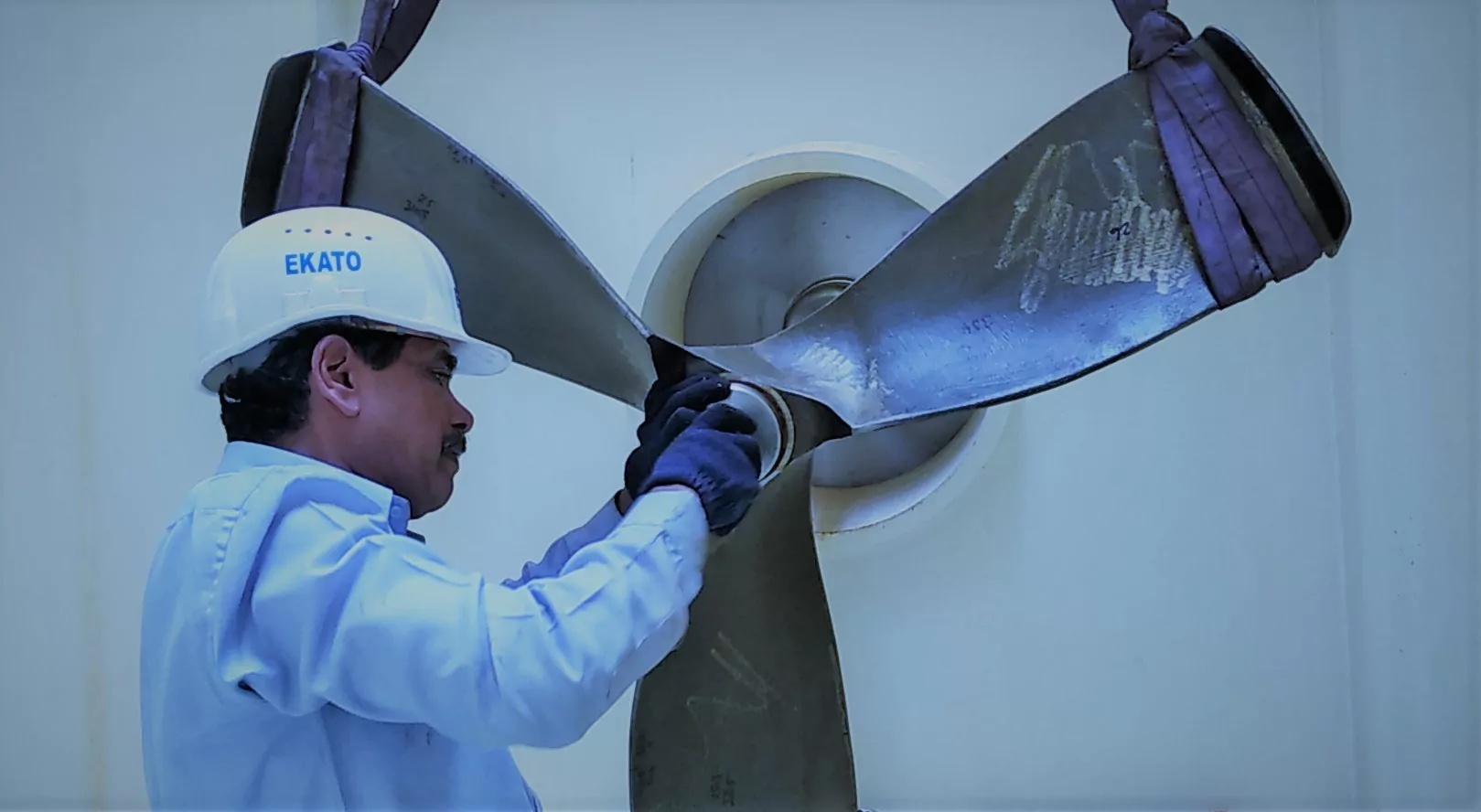
Field Service
Installation, commissioning, inspection and maintenance - with our support for the best result!
What we Offer
Installation and commissioning of EKATO agitators
From planning to commissioning
Agitators
The service on our agitators usually includes the following activities:
Process plants
Unlike agitators, the EKATO Group’s process plants are supplied complete with control system and operating software. The commissioning of such a system is therefore slightly different compared to that of a normal agitator. In these cases, EKATO offers extended support during commissioning.
The commissioning of the process systems is accompanied by a process engineer, for example from research and development.
This includes a test run in water and an I/O test. The system is then checked together with you in accordance with the functional description. EKATO accompanies you during the first batches and supports you in optimizing parameters and limit values. Together with you, process conditions are analyzed and optimized wherever possible.
On-site inspection and maintenance
We ensure that your agitators, mechanical seals and supply systems are always in perfect condition!
We provide you with active support on site:
You will receive a service report including a maintenance recommendation for the next inspection. We will also be happy to support you directly with a suitable spare parts offer or with the creation of a maintenance concept for your agitators.
Carrying out gearbox and sealing fluid changes, as well as replacing spare and wear parts. This also includes cleaning and checking important components, such as the mechanical seal. This also includes cleaning and checking important components such as the mechanical seal.
In the event of a problem, we will be happy to help you over the phone or support you directly on site with troubleshooting and rectification.
Vibration measurements and thermography can be used to analyze and evaluate various damage patterns and operating anomalies. The information obtained is assessed, evaluated and discussed with you by our specialists.
Repairs
And when things have to be done quickly…
…we also support you on site in the event of unplanned breakdowns and repairs to get your agitator up and running again as quickly as possible!
In such cases, please get in touch directly with our contact persons listed below.
Alternatively, your repairs can also be carried out directly at our headquarters. Find out more about this:
Remote maintenance support from our service technicians
On-site support from a service technician is not always possible, for example due to the COVID-19 virus and the associated travel and contact restrictions. For these special circumstances, we offer our innovative “Remote Service Support” to replace on-site support in the best possible way. In the event of commissioning, the customer is guided and instructed by our trained specialist staff using the latest technology.
This ensures smooth commissioning and acceptance of our products. In addition, this option is used to maintain the training of regional service technicians worldwide, which previously took place at the head office.
which previously took place at the head office. In this way, we can also ensure our high quality standards in this area.
Advantages
We offer our remote service support with our own TeamViewer Pilot software. However, we are flexible and can also use software of the customer’s choice if required.
On-site training for your service technicians
Hands-on and small training courses
We also offer short hands-on training sessions for your mechanics as part of our service calls.
Our technician will discuss the basics of the agitator type, maintenance intervals and safety instructions.
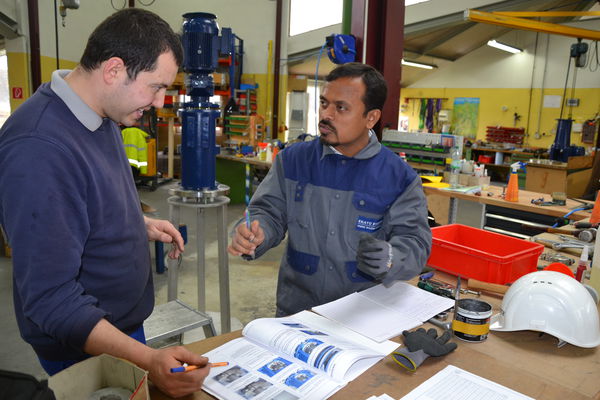
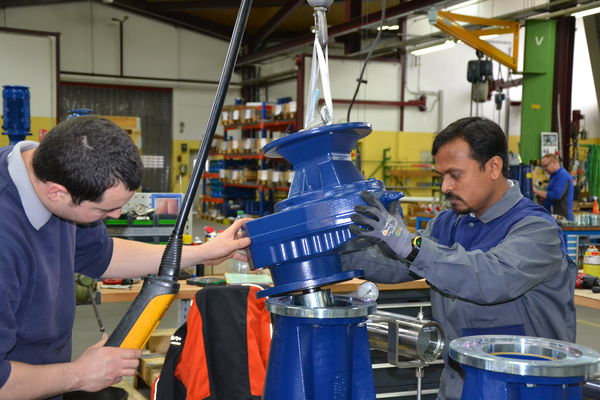
Your Benefits
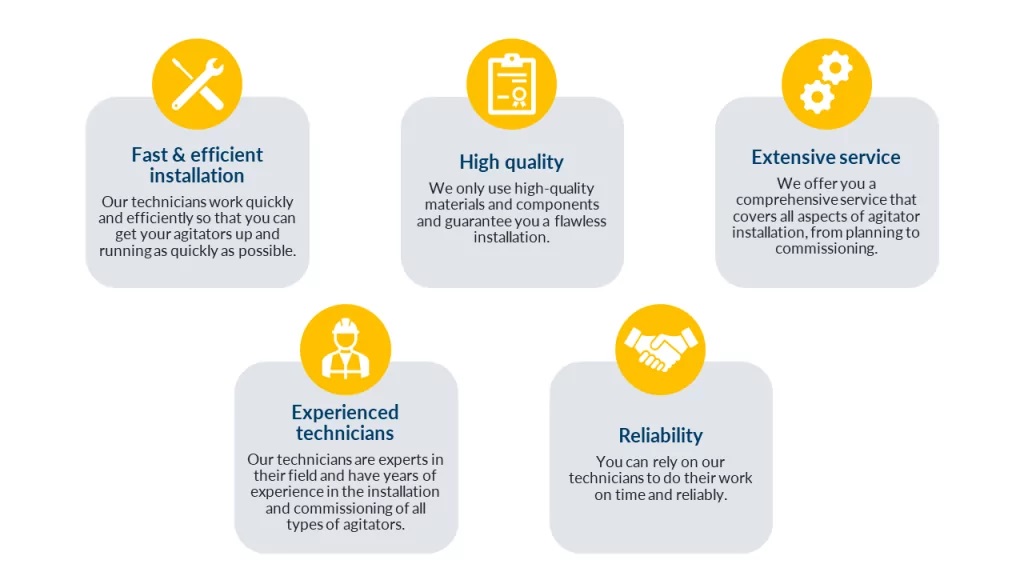

Head of Field Service
EKATO Rühr- und Mischtechnik GmbH
+49 7622 29 -525
lother.waller@ekato.com
.
Your contact for field service
Do you have any questions or need information about our services?
We would be happy to talk to you personally!
Book a non-binding consultation for free.